Sand and Gravel Quarry Crushing Machinery Costs
Quarries that produce sand and gravel rely heavily on specialized crushing machinery to process raw materials efficiently and cost-effectively. From crusher and conveyors to screens and feeders, every piece of machinery plays a vital role in transforming extracted rock and gravel into saleable, high-quality aggregate. However, acquiring and maintaining this equipment is a significant investment. Understanding the costs associated with quarry machinery—both direct and indirect—can aid quarry operators in optimizing their production costs, improving profitability, and remaining competitive in the market.
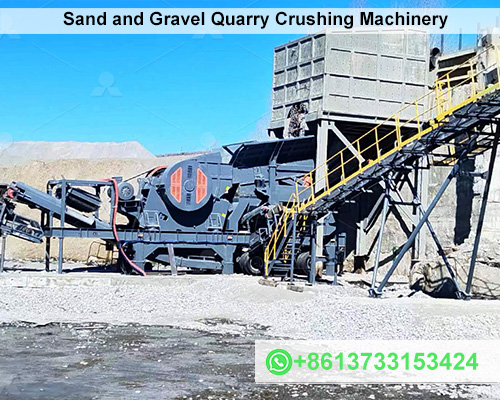
1. Types of Crushing Machinery in Sand and Gravel Quarries
To comprehend the costs involved, it’s essential to know the types of machinery used in a sand and gravel quarry. Common equipment includes:
- Jaw Crusher: Primarily used for primary crushing to reduce large boulders into manageable sizes.
- Cone Crusher: Ideal for secondary or tertiary crushing, creating finer, uniform aggregate.
- Impact Crusher: These machines are often used for softer materials and are ideal for producing sand and smaller gravel.
- Gyratory Crusher: Similar to cone crusher, these can handle high-throughput applications and large feed sizes.
- Screens and Vibrating Feeders: These separate and distribute materials according to size, ensuring that only suitable material progresses through the crushing process.
- Conveyors and Feeders: Essential for moving material across different stages of the crushing process, improving efficiency.
Each machine type has its specific function, operating cost, and purchase price, which directly influence the overall investment.
2. Initial Machinery Purchase and Installation Costs
The initial purchase and installation costs for crushing machinery can vary widely. Some cost factors include:
- Type of Machinery and Capacity: Crusher with higher capacities (like gyratory or high-powered cone crusher) can cost significantly more than smaller jaw crusher.
- Brand and Quality: Premium brands often have higher upfront costs but may offer greater durability and less downtime.
- Transport and Installation: Transportation costs depend on the distance from the manufacturing site to the quarry, and installation often requires specialized engineers.
Generally, initial costs for quarry crushing machinery can range from $100,000 to over $1 million, depending on capacity, brand, and customization.
3. Operating and Maintenance Costs
After installation, the cost of keeping machinery operational is critical. Key elements of operating costs include:
- Fuel and Energy Consumption: Diesel and electricity are major expenses, particularly for heavy-duty machinery. Crusher, feeders, and conveyors consume considerable power to operate.
- Wear and Tear on Parts: Regular use in harsh quarry conditions leads to frequent wear, especially on crusher jaws, hammers, and screens. Replacement parts, especially those with high-grade alloy materials, can be costly.
- Lubrication and Fluids: Regular lubrication and hydraulic fluid replacement are necessary to prevent machinery breakdowns.
- Labor Costs: Skilled labor is essential for operating, maintaining, and troubleshooting quarry machinery. Operators, technicians, and mechanics’ wages contribute to operating costs.
Operating and maintenance costs can be significant, often accounting for 15-30% of total operational expenses annually. By adopting a proactive maintenance schedule, quarry operators can mitigate unexpected repairs and reduce downtime.
4. Depreciation and Financing
Quarry machinery typically has a long but finite operational lifespan. Depreciation and financing costs include:
- Depreciation: Heavy machinery depreciates over time, with some equipment losing value faster due to wear. Depreciation can be calculated on a straight-line basis or using accelerated methods, depending on the accounting approach.
- Interest and Loan Repayments: Many quarries finance machinery purchases. Financing costs vary depending on interest rates, down payments, and loan terms.
The combination of depreciation and financing can add a substantial amount to the overall cost of crushing machinery, impacting cash flow and tax obligations.
5. Regulatory and Environmental Compliance Costs
Environmental regulations often require quarry operators to invest in dust suppression, noise control, and energy-efficient machinery to minimize their environmental impact. Some common expenses include:
- Dust Control Systems: Misting and water-spray systems help suppress dust, a common byproduct of crushing operations. These systems add both capital and operating costs.
- Noise Reduction: Acoustic enclosures or noise-dampening features may be required, adding to the initial investment and upkeep costs.
- Environmental Monitoring and Permits: Compliance often entails regular monitoring and maintenance to adhere to emissions standards, which can incur fines if neglected.
6. Cost Analysis and Optimizing Machinery Investment
A thorough cost analysis should consider all stages of machinery investment, including purchase, operation, maintenance, and compliance. Here are some tips for cost optimization:
- Choosing the Right Equipment for Application: Selecting appropriate machinery for the intended material and production rate can avoid unnecessary expenses on oversized or underperforming equipment.
- Implementing Preventative Maintenance Programs: Regular inspections and scheduled maintenance can extend the life of crusher, conveyors, and screens, reducing the need for expensive repairs.
- Exploring Energy-Efficient Options: Energy-efficient machinery or renewable energy sources can reduce fuel costs and improve the environmental profile.
- Training and Skilled Labor: Properly trained operators and maintenance staff ensure efficient machinery use, reducing wear and optimizing production rates.
Conclusion
Investing in and maintaining sand and gravel crushing machinery is a significant cost center for quarry operators. By understanding the full spectrum of initial, operational, and maintenance costs, quarries can make more informed decisions to maximize their return on investment. Optimizing machinery selection, implementing preventive maintenance, and exploring cost-effective financing and compliance measures are essential to ensuring a profitable and efficient quarry operation.