Technical knowledge of vsi vertical shaft impactor
Vertical Shaft Impactors (VSI) are one of the most efficient equipment for producing high-quality aggregates, sand, and other materials used in various industrial sectors like construction, mining, and recycling. With its ability to create precise shapes and sizes, the VSI has become essential in shaping and improving the quality of material produced. This article explores the technical knowledge of VSI, including its working principles, key components, and applications.
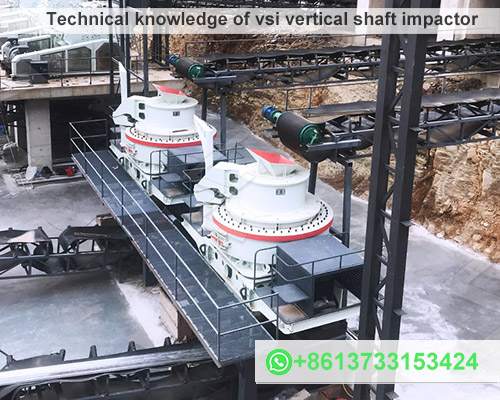
Working Principle of VSI
At the core of the VSI is the process of rock-on-rock crushing. Unlike traditional crusher, which rely on high-impact force to break down materials, the VSI uses centrifugal force and velocity to fragment the feed material. Here’s how it works:
- Material Feed: The feed material is introduced into the center of the rotor through a vertical feed tube.
- Acceleration: Once inside, the material is accelerated by the rotor’s centrifugal force, reaching speeds of up to 80 m/s.
- Impact: The high-velocity material is projected against a stationary surface, usually an anvil or a bed of the same material (autogenous crushing). The resulting impact shatters the material into smaller particles.
- Particle Size Control: The final size of the material is controlled by adjusting the rotor speed, feed rate, and the design of the crushing chamber.
This rock-on-rock crushing mechanism is known for producing cubically shaped particles with uniform gradation, making it ideal for industries requiring fine materials, such as concrete production.
Key Components of VSI
The VSI consists of several critical components that work together to ensure efficient operation. The following are the key parts of a VSI machine:
- Rotor: The rotor is the heart of the VSI. It accelerates the feed material to high velocity and propels it toward the crushing chamber. Different rotor designs are available, depending on the application and desired product size.
- Feed Tube: The vertical feed tube is responsible for directing the material into the rotor. It ensures the material is fed at the right angle and speed to achieve optimal crushing results.
- Crushing Chamber: The crushing chamber, also known as the anvil or autogenous chamber, is where the impact occurs. The design and configuration of the chamber can significantly affect the final product size and shape.
- Drive Mechanism: The drive mechanism, usually powered by an electric motor, is responsible for rotating the rotor at high speeds. Properly sized motors ensure efficient energy use and reduced wear on the machine.
- Wear Parts: VSI machines are equipped with replaceable wear parts, such as anvils, liners, and rotor tips. These parts are critical to the machine’s durability and operational longevity.
Types of VSI Crushers
There are different types of VSI crusher, each designed for specific applications:
- Autogenous VSI Crushers: These crusher rely on the rock bed within the machine for impact and wear, making them highly efficient in producing shaped material without additional wear costs.
- Semi-Autogenous VSI Crushers: These models use both rock-on-rock and rock-on-metal crushing techniques, providing flexibility for producing different types of materials.
- Standard VSI Crushers: These crusher employ metal anvils for impact, which increases the production of fines and improves control over product size.
Applications of VSI
The versatility of the VSI makes it an integral tool in various industries. Some common applications include:
- Aggregates Production: VSI is widely used in the production of high-quality aggregates for asphalt, concrete, and road construction. The cubical shape of the aggregates produced enhances the strength of the final product.
- Manufactured Sand: With natural sand becoming increasingly scarce, VSI has become crucial in the production of artificial sand. It allows for precise control over the particle size and distribution, ensuring the manufactured sand meets stringent quality standards.
- Mining: In the mining industry, VSI crusher are used to crush ores and minerals, improving their liberation and reducing the energy required for further processing.
- Recycling: VSI machines are employed in recycling operations to process various materials like glass, ceramics, and concrete. They help reduce landfill waste by creating reusable materials.
- Industrial Minerals: VSI crusher are commonly used to process industrial minerals like calcium carbonate, gypsum, and phosphate, ensuring the desired particle size and consistency for various applications.
Advantages of VSI
- High Efficiency: VSI crusher offer high crushing efficiency, producing more output with lower energy consumption compared to traditional crusher.
- Better Particle Shape: The rock-on-rock crushing action ensures the production of cubical-shaped particles, which improve the quality of aggregates used in construction.
- Versatility: VSI crusher can handle a wide range of materials, from soft to hard, making them suitable for various industrial applications.
- Cost-Effective: With replaceable wear parts and low energy requirements, VSI crusher provide a cost-effective solution for producing high-quality materials.
- Environmental Benefits: The ability to produce manufactured sand reduces the demand for natural sand, contributing to the preservation of natural resources and promoting sustainable construction practices.
VSI (Vertical Shaft Impactor) crusher play a pivotal role in the production of high-quality aggregates, manufactured sand, and other materials used in various industries. Their efficiency, versatility, and ability to produce cubically shaped particles make them essential in modern-day construction, mining, and recycling operations. Understanding the technical aspects of VSI technology can help businesses optimize their processes and achieve superior results.