600t/h Aggregate Crushing Plant In Thailand
Thailand’s fast growing economy that leads to a boom in the construction which increases the demand of aggregates. Silisomboonsub is one company that mainly produces limestone aggregate for construction while its other mine is producing about 200t/h of granite aggregate. New granite crushing plant is designed, Among three crushing circuit, the first crushing circuit produces 48% of ballast, 17% of -25+9mm, 4% of -9+4.8mm, 6% of -4.8mm, and 25% of -40mm products. While a Jaw C120 is operated at 84% load with feeding speed 600t/h, a secondary HP300 cone crusher (cavity std extra coarse, setting 60mm) operated at 78% load, and a tertiary cone crusher HP200 (cavity std coarse, setting 40mm) is operated at 67% load.
1. Primary Crushing Stage
Granite with standard solid density, crushability, abrasiveness of 2.7t/m3, 35%, 1398g/t, respectively,used with feeding speed 600t/h. Jaw crusher C120 with 135mm CSS is operated at 84% Load. Grizzly Feeder VF561-2V with 90mm opening is operated under 62% load and tk deck having separation of 28mm with efficiency of 43% are configured.
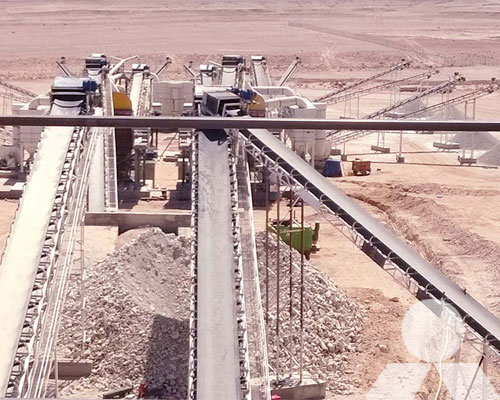
2. Secondary and Tertiary Stages
• First circuit
From surge pile, crushed granite is fed at speed 500t/h into secondary and tertiary cone crushers after screening using CVB203P. Undersize product, -40mm, is mix aggregate product (25% of production), and -63+40mm product is transported to tertiary cone crusher HP200 (cavity std coarse, setting 40mm) operated at 67% load. The oversize production (+63mm) is transported to secondary cone crusher HP300 (cavity std extra coarse, setting 60mm) operated at 78% load. Reduction ratio in cone HP300 and HP200 are 2.2 and 1.8, respectively. CVB203P is CVB screen for primary screening with three decks: 100mm,63mm, 40mm in respect to 87%, 93%, 93% efficiency. CVB203 is used to screen products from secondary cone HP300 where oversize product, +63mm, is circulated back to tertiary cone HP200, -63mm+25mm product is separated out, and undersize products (-25mm+9mm and -9mm) is transported to the next screen. CVB202 is used as final product screen where 1st deck (9mm separation) and 2nd deck (4.8mm separation) are 95% effective. From this circuit, -63+25mm, -25+9mm, -9+4.8mm, -4.8mm products are 48%, 17%, 4%, and 6% of production, respectively.
• Second circuit
Similar to 1st crushing circuit, CVB203P is operated at the same efficiency for all decks. Oversize product, +100mm, is fed into secondary cone HP300 (cavity std extra coarse, setting 60mm) operated at 45% load. -100+63mm product is fed into tertiary cone HP300 (cavity std coarse, setting 30mm) operated at 60% load. -63+40mm product is transported directly to CVB203 screen, leaving undersize product, -40mm, as mix aggregate product (25%). Reduction ratio secondary is 2.5 and tertiary is 2.6. oversize product from screen CVB203 is circulated back into tertiary. Each screen decks (CVB203 and CVB202) can separate product with 95%, 89%, 91%, 94%, and 94% efficiency, respectively. The product are -63+25mm (48%), -25+9mm(17%), -9+4.8mm (3%), -4.8mm (6%).
• Third circuit
Undersize product from screen CVB203P is separated as mix aggregate product (25% of production), -63+40mm product is transported to screen CVB202, and the oversize +63mm is fed into secondary cone HP300 (cavity std extra coarse, setting 60mm) that operated at 67% load. Ballast product is separated from CVB202 while oversize and undersize product (-25mm, +63mm) are fed into tertiary cone HP300 (cavity std medium, setting 20mm) operated at 84% load. Product from tertiary cone HP300 is screen with CVB203 with decks apertures 19mm, 9mm, 4.8mm and efficiency of 95%, 89%, 85%, respectively. The oversize (+19mm) is circulated back into tertiary cone HP300. The Products are 44% Ballast, 15% product -19+9mm, 6% product -9+4.8mm, 11% product -4.8mm.