Gravel Making Machine
Gravel is a crucial material used in construction, landscaping, road building, and various other infrastructure projects. A gravel making machine, often called a crusher or stone crusher, is an essential piece of equipment in producing gravel for these applications. These machines break down large rocks, stones, and other materials into smaller, more manageable pieces, or specific sizes of gravel.
In this article, we will explore the function of gravel making machines, their types, and the specific applications in which they are used.
1. What is a Gravel Making Machine?
A gravel making machine is designed to crush and process raw stone material into gravel, which is then used in a variety of industries. The machine typically operates through mechanical force, breaking down large rocks or boulders into smaller fragments. Gravel can be produced in different grades, depending on the size of the output and the specific needs of the project.
These machines are vital for providing a consistent, high-quality gravel supply that meets construction standards.
2. Key Components and Working Principle
Gravel making machines rely on various mechanical and technological components to carry out their tasks effectively. The general working principle involves:
- Feeding System: Large rocks or raw materials are loaded into the machine via feeders. These feeders can be vibrating or belt conveyors that regulate the flow of materials into the crushing chamber.
- Crushing Mechanism: Once the raw material enters the crusher, it is subjected to mechanical pressure and impact forces that reduce its size. The crushing mechanism varies depending on the type of gravel making machine, with some machines using compression forces (like jaw crushers), while others rely on impact or shear forces.
- Screening System: After the materials are crushed, the resulting product may pass through a screening system to sort gravel by size. This ensures the output meets specific size requirements for different applications.
- Discharge System: The final product is discharged and collected for further use. The size of the gravel can be adjusted by configuring the machine settings to meet desired specifications.
3. Types of Gravel Making Machines
There are several types of gravel making machines, each suited for different types of materials and desired output sizes. The most common types include:
3.1 Jaw Crusher
Jaw crushers are widely used in gravel production because of their simplicity and ability to handle hard, abrasive materials. These machines work by compressing large rocks between two plates (jaws), one stationary and one that moves. As the rocks are crushed, they break down into smaller pieces.
Advantages:
- Suitable for hard materials like granite or basalt.
- Simple design and low operational costs.
- Produces uniform gravel sizes.
Disadvantages:
- Can produce elongated or flaky gravel, which may need further processing.
3.2 Cone Crusher
Cone crushers are used for secondary or tertiary crushing, particularly when high-quality, well-shaped gravel is required. They work by squeezing the material between a rotating cone and a fixed outer bowl. Cone crushers are particularly effective for producing finely graded gravel.
Advantages:
- High production efficiency.
- Suitable for hard and medium-hard materials.
- Produces cubical gravel that is ideal for concrete and asphalt applications.
Disadvantages:
- Higher maintenance requirements due to their more complex design.
3.3 Impact Crusher
Impact crushers break down materials through the use of impact forces. They feature rotating hammers or blow bars that strike the material, causing it to fracture along natural fault lines. These crushers are especially useful for producing gravel with irregular shapes and softer materials like limestone or recycled concrete.
Advantages:
- Ideal for producing finely crushed gravel.
- Works well with soft to medium-hard materials.
- Good for producing gravel for road surfaces and concrete production.
Disadvantages:
- Not suitable for very hard materials.
- Can create a higher amount of fines (small particles).
3.4 Vertical Shaft Impact Crusher (VSI)
A VSI crusher operates by accelerating materials through a high-speed rotor and then ejecting them into a crushing chamber. This mechanism results in materials being crushed by impact, and VSI machines are commonly used to produce high-quality gravel with a uniform shape.
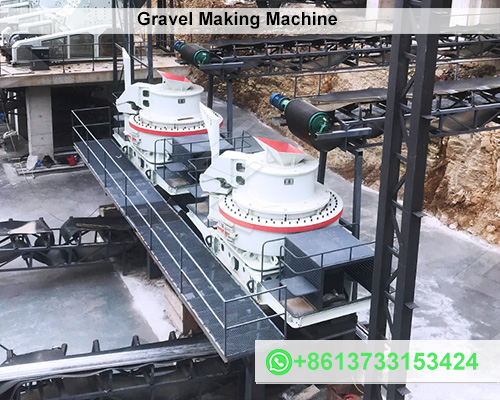
Advantages:
- Produces finely shaped gravel.
- Ideal for sand and gravel production.
- High efficiency in generating precise output sizes.
Disadvantages:
- More suitable for medium to soft materials.
- Energy-intensive compared to other crushers.
3.5 Hammer Mill Crusher
Hammer mill crushers are designed for crushing softer and lighter materials. They operate using hammers attached to a rotating shaft, which strikes and shatters the material.
Advantages:
- Good for materials like limestone and coal.
- Produces uniform gravel size with consistent output.
Disadvantages:
- Limited to softer materials.
- Not ideal for high-volume gravel production.
4. Applications of Gravel Making Machines
Gravel making machines play a critical role in a variety of industries and projects. Some key applications include:
4.1 Construction
Gravel is a vital material for building foundations, concrete mixes, and drainage systems. Construction companies rely on gravel making machines to supply the necessary amount of gravel in various sizes, from coarse aggregates to fine fillers.
- Road Construction: Gravel is a common material used in the base layer of roads and highways. It provides a solid foundation and helps with water drainage, making the road surface durable and long-lasting.
- Concrete Production: In ready-mix concrete, gravel is used as an aggregate to give the concrete its strength and structure.
4.2 Landscaping
In landscaping projects, gravel is often used for driveways, garden paths, decorative edging, and water features. Gravel making machines provide the specific size and type of gravel needed for various aesthetic and functional purposes in outdoor spaces.
4.3 Mining and Quarrying
In the mining and quarrying industries, gravel making machines help process raw stone material into crushed aggregates. These materials are used for a wide range of purposes, including ore processing and site preparation.
4.4 Infrastructure and Civil Engineering
Gravel is an essential component in various civil engineering projects, including drainage systems, embankments, and retaining walls. Gravel making machines ensure that civil engineers have a steady supply of the necessary material for these projects.
5. Maintenance and Efficiency
Maintaining gravel making machines is vital to ensure efficiency and longevity. Routine maintenance includes checking wear parts like hammers, jaws, or rotors, and replacing them when necessary. Regular lubrication and monitoring of belts, bearings, and motors can also prevent breakdowns. Preventive maintenance extends the life of the machine and ensures a steady output of high-quality gravel.
Conclusion
Gravel making machines are essential in producing gravel for a wide range of industries and construction applications. With various types available, such as jaw crushers, cone crushers, impact crushers, and VSI machines, manufacturers can tailor their equipment to produce gravel that meets specific project requirements. These machines play a key role in infrastructure development, mining, landscaping, and other critical sectors. By selecting the right type of gravel making machine and maintaining it properly, companies can ensure consistent, high-quality gravel production for their needs.