Designing a Sand and Gravel Processing Plant
Sand and gravel are essential construction materials that underpin a wide range of applications, from concrete and asphalt to road construction and landscaping. The design of a sand and gravel processing plant plays a critical role in ensuring the production of high-quality aggregates that meet industry standards and customer specifications.
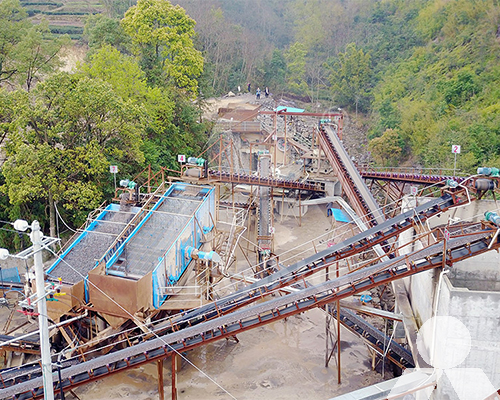
Key Considerations for Sand and Gravel Processing Plant Design
Designing an efficient and productive sand and gravel processing plant requires careful consideration of several factors:
1. Feed Material Characteristics:
- Understanding the properties of the raw feed material, including its particle size distribution, hardness, and abrasiveness, is crucial for selecting the appropriate processing equipment.
2. Product Requirements:
- The desired product specifications, such as particle size ranges, gradation, and purity, dictate the necessary processing stages and equipment configurations.
3. Plant Capacity and Throughput:
- Determining the required plant capacity and throughput ensures that the processing system can meet production demands without bottlenecks or inefficiencies.
4. Space Constraints and Layout:
- The available plant area and desired layout influence the arrangement of equipment, material flow paths, and storage facilities.
5. Environmental Regulations:
- Compliance with environmental regulations regarding dust emissions, noise control, and water usage requires the integration of appropriate pollution control measures.
Essential Components of a Sand and Gravel Processing Plant
A typical sand and gravel processing plant comprises several key components:
1. Feeding System:
- The feeding system, often consisting of feeders or conveyors, introduces raw material into the processing stream.
2. Crushing Stage:
- crusher, such as jaw crusher, gyratory crusher, or cone crusher, break down oversized rocks into smaller pieces.
3. Screening Stage:
- Screens, including vibrating screens and trommel screens, separate the crushed material into different particle sizes based on sieve openings.
4. Washing Stage:
- Washers, such as log washers or screw washers, remove impurities and contaminants from the aggregate using water.
5. Classification Stage:
- Classifiers, such as spiral classifiers or hydrocyclones, further separate fine particles based on their settling velocities in water.
6. Conveying and Storage:
- Conveyor belts transport processed materials to storage bins or stockpiles, ensuring continuous operation and product availability.
7. Control and Monitoring Systems:
- Control and monitoring systems regulate equipment operation, material flow, and product quality, ensuring efficient and consistent production.
Design Optimization for Sand and Gravel Processing Plants
Optimizing the design of a sand and gravel processing plant involves:
1. Process Flow Optimization:
- Analyzing and optimizing the material flow path minimizes handling and transportation distances, reducing energy consumption and wear and tear on equipment.
2. Equipment Selection:
- Selecting the most suitable equipment based on feed material properties, product requirements, and capacity demands ensures efficient operation and product quality.
3. Automation and Control:
- Implementing automation and control systems enhances process efficiency, reduces labor requirements, and improves product consistency.
4. Environmental Considerations:
- Integrating dust suppression systems, noise control measures, and water treatment facilities minimizes environmental impact and promotes sustainable practices.
Designing a sand and gravel processing plant requires careful consideration of various factors, from feed material characteristics to product requirements and environmental regulations. By optimizing process flow, selecting appropriate equipment, and implementing advanced control systems, modern sand and gravel processing plants can achieve high efficiency, product quality, and environmental sustainability.