The Most Popular Crusher in Basalt Production Industry
In the basalt production industry, one of the most popular crushers is the jaw crusher. Jaw crushers are widely used for primary crushing of various materials, including basalt, due to their high efficiency, reliability, and versatility.
Here are some reasons why jaw crushers are commonly used in the basalt production industry:
High crushing ratio: Jaw crushers have a large feed opening and a deep crushing chamber, which allows them to handle large-sized basalt rocks. They have a high crushing ratio, meaning that they can produce a high percentage of fine and uniform-sized particles.
Strong and durable construction: Basalt is a hard and abrasive material, and jaw crushers are designed to handle such challenging conditions. They are constructed with strong and durable materials, such as high-quality steel, which ensures their longevity and reliable performance in crushing basalt.
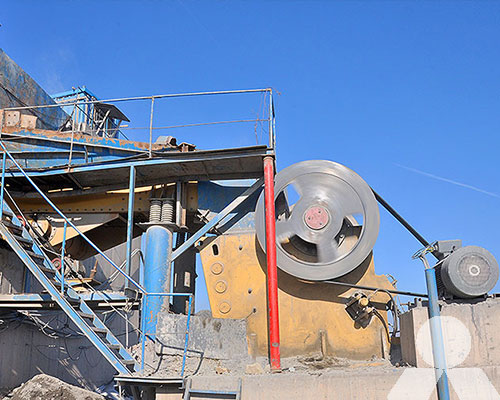
Adjustable discharge setting: Jaw crushers have a movable jaw plate that can be adjusted to control the size of the output material. This feature allows operators to produce various sizes of crushed basalt according to their specific requirements.
Simple operation and maintenance: Jaw crushers have a straightforward design, making them easy to operate and maintain. They typically have a simple structure, fewer moving parts, and fewer components that require regular maintenance. This makes jaw crushers suitable for continuous and efficient production in the basalt industry.
Versatility: Jaw crushers are versatile machines that can handle a wide range of materials, not just basalt. They can be used for various applications in the mining, construction, and recycling industries. This versatility makes jaw crushers a popular choice for different stages of basalt production, from primary crushing to secondary or tertiary crushing.
While jaw crushers are widely used in the basalt production industry, it’s worth noting that other crushers, such as cone crushers and impact crushers, can also be suitable depending on the specific requirements of the production process. Cone crushers are often used for secondary or tertiary crushing, while impact crushers are known for their high reduction ratios and ability to produce cubical-shaped particles. The choice of crusher ultimately depends on factors such as the desired final product size, production capacity, and specific application requirements.