Primary Crusher for Gold Ore
Gold ore, often embedded in hard rock formations like quartz or sulfide deposits, requires robust primary crushing to liberate gold particles for further processing. Choosing the right primary crusher for gold ore is critical to reduce energy costs, minimize downtime, and enhance recovery rates. This guide explores the top crusher types, selection strategies, and operational best practices.
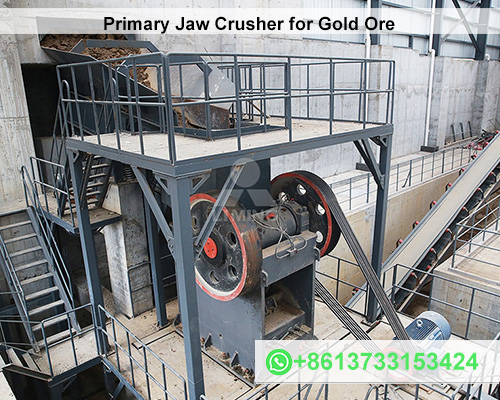
Why Primary Crushing Matters in Gold Processing
Primary crusher break down large gold-bearing rocks (≤1.5 m) into manageable fragments (≤150 mm). Key objectives include:
- Liberating gold particles from host rock.
- Reducing load on secondary crusher (e.g., cone crusher).
- Minimizing energy consumption in downstream processes like grinding.
Top 3 Primary Crusher for Gold Ore
1. Jaw Crusher
- Mechanism: Compressive force via a fixed and movable jaw plate.
- Best For: High-grade ore with moderate abrasiveness (e.g., quartz veins).
- Recommended Models:
- Liming C6X110: Handles up to 500 t/h with a 1,500 x 1,070 mm feed opening.
- PE 1000*1200 Jaw Crusher: Energy-efficient design with optional hybrid power.
2. Gyratory Crusher
- Mechanism: Rotating mantle against a concave liner.
- Best For: Large-scale mines with high-capacity demands (1,000+ t/h).
- Advantage: Lower maintenance costs over time vs. jaw crusher.
3. Mobile Jaw Crusher
- Mechanism: Compact jaw crusher mounted on tracks or wheels.
- Best For: Remote or temporary gold mining sites.
- Example: NK PE3040 with a 1,065 x 550 mm jaw and 350 t/h capacity.
How to Choose the Right Primary Crusher
Factor | Guidelines |
---|---|
Ore Hardness | Use jaw crusher for Mohs 5-6 (quartz). Gyratory crusher for harder sulfides. |
Feed Size | Ensure crusher opening accommodates largest rock (e.g., 1.5 m rocks need ≥1.6 m opening). |
Throughput | Match crusher capacity to mine output (e.g., 200 t/h for small operations). |
Mobility Needs | Mobile crusher reduce haulage costs in dispersed deposits. |
Maintenance Access | Prioritize designs with easy liner replacement (e.g., reversible jaw plates). |
4 Best Practices to Optimize Primary Crushing
- Pre-Screening
Remove fine materials (<50 mm) before crushing to reduce wear and improve efficiency. - Liner Material Selection
Use manganese steel (14-18% Mn) for abrasion resistance in quartz-heavy ore. - Regular Gap Adjustment
Maintain optimal jaw/gyratory crusher settings to ensure consistent output size. - Dust Suppression
Install water sprays or enclosures to protect equipment and workers in dry climates.
Case Study: Boosting Gold Recovery in Nevada
A gold mine in Nevada replaced an aging jaw crusher with a Sandvik CJ815 gyratory crusher, achieving:
- 25% higher throughput (from 300 t/h to 375 t/h).
- 40% reduction in liner replacement costs due to improved wear resistance.
- 12% increase in gold recovery from optimized particle size distribution.
Maintenance Checklist for Gold Ore Crusher
- Daily: Inspect hydraulic systems and check for abnormal vibrations.
- Weekly: Lubricate bearings with high-temperature grease (NLGI Grade 2).
- Monthly: Measure jaw/concave wear; replace if thickness loss exceeds 30%.
- Annually: Overhaul the eccentric shaft and bushings.
Cost Considerations
- Jaw Crusher: 150,000–150,000–150,000–600,000 (depending on size and features).
- Gyratory Crusher: 500,000–500,000–500,000–2.5M (ideal for large-scale operations).
- Mobile Crusher: 200,000–200,000–200,000–1M (includes mobility and setup flexibility).
Tip: Leasing mobile crusher can cut upfront costs for short-term projects.
Conclusion
Selecting the right primary crusher for gold ore hinges on ore characteristics, operational scale, and long-term cost efficiency. Jaw crusher excel in versatility, while gyratory crusher dominate high-capacity scenarios. Always partner with manufacturers offering onsite support and wear-resistant component guarantees.