Ball Mill and Crusher for Iron Ore in Mineral Processing
Iron ore is one of the most important minerals in the world, serving as the primary raw material for steel production. As demand for steel continues to grow globally, efficient and reliable processes for extracting iron from its ore become crucial. Two critical pieces of equipment used in this process are the ball mill and the crusher. These machines play vital roles in the crushing, grinding, and refinement of iron ore, enabling it to be processed further into iron products. This article explores the functions, differences, and applications of ball mills and crusher in the iron ore industry.
Crusher for Iron Ore
Purpose and Functionality
A crusher is the first step in iron ore processing. It reduces large chunks of raw ore into smaller, manageable pieces. Crusher vary in size and design but share a common purpose: to apply force to break down rock into smaller fragments.
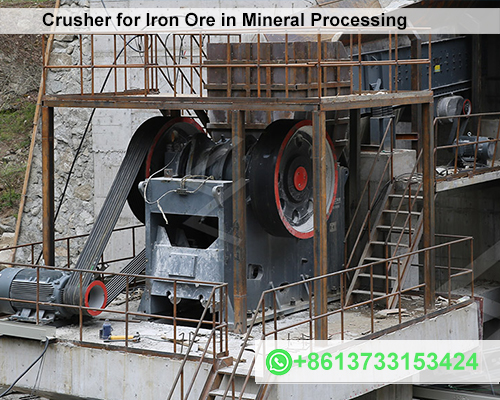
Types of Crusher
- Jaw Crusher: These machines use compressive force to crush large blocks of ore. A fixed and a moving jaw plate create a “crushing chamber” where the ore is compressed and broken down. Jaw crusher is highly durable and suitable for primary crushing of hard materials like iron ore.
- Gyratory Crusher: Another primary crusher used in iron ore processing, gyratory crusher feature a concave surface and a conical head. The ore is fed into the chamber and crushed by the circular motion of the head.
- Cone Crusher: These crusher is typically used for secondary crushing after the initial size reduction. Cone crusher work by crushing iron ore between a rotating cone and a stationary concave. This machine provides fine crushing and helps achieve the desired particle size.
- Impact Crusher: Though less common in iron ore processing, impact crusher use impact force to break materials by projecting them against metal surfaces at high speeds. They are typically used for softer materials but can be effective for iron ore with the right design.
Role in Iron Ore Processing
In iron ore processing, crusher help reduce the size of the mined material. This is essential because:
- The ore needs to be small enough to be transported for further processing.
- Crushing helps liberate the valuable iron content from surrounding waste material (gangue), improving the efficiency of later stages like grinding and beneficiation.
Ball Mill for Iron Ore
Purpose and Functionality
Once the ore has been reduced to smaller pieces by the crusher, it is further ground into finer particles in a ball mill. A ball mill is a type of grinder that uses rotating steel or ceramic balls to break down material into a fine powder or slurry.
Working Principle
The ball mill consists of a rotating drum filled with grinding media (steel balls) and the ore. When the mill rotates:
- The balls tumble and crush the iron ore.
- The constant motion causes impact, abrasion, and shear forces that grind the ore into a finer consistency.
Ball mills come in different sizes and capacities and are often categorized into two types:
- Dry Ball Mills: Suitable for dry material grinding, typically used when water or moisture-sensitive materials are involved.
- Wet Ball Mills: These are more common in iron ore processing and are used when the ore is mixed with water to create a slurry for further refining.
Role in Iron Ore Processing
Grinding is an essential step in iron ore processing, and ball mills offer the following advantages:
- Fine Grinding: Ball mills can grind iron ore to extremely fine powders, crucial for enhancing the efficiency of subsequent steps like flotation, magnetic separation, or direct reduction processes.
- Size Reduction: Ore must be reduced to fine particles before the iron can be extracted. Ball mills ensure the iron ore is processed to the correct size for further beneficiation techniques.
- Optimized Liberation: The ball mill’s grinding process helps separate valuable iron from impurities or unwanted materials by breaking the ore particles down and exposing the iron.
Ball Mill vs. Crusher: Differences in Functionality
While both ball mills and crusher is essential in iron ore processing, they serve distinct roles:
- Primary Crushing (Crusher): The crusher breaks down large blocks of iron ore into smaller fragments, making it easier to handle for further processing. Crusher typically deal with coarse materials.
- Grinding and Size Refinement (Ball Mill): The ball mill is responsible for grinding the ore to finer particles, preparing it for further separation processes like magnetic separation or flotation. Ball mills focus on fine grinding, handling the material after the initial crushing stages.
Applications of Crusher and Ball Mills in Iron Ore Processing
- Mining Operations: Crusher and ball mills are standard equipment in mining sites where raw iron ore is extracted. Crusher handle the primary size reduction, while ball mills refine the material for beneficiation.
- Steel Manufacturing: Steel manufacturers use ball mills and crusher to prepare iron ore for smelting. By breaking down the raw material and refining it, these machines help produce high-quality iron for steelmaking.
- Beneficiation Plants: In facilities focused on ore beneficiation, crusher and ball mills are used to prepare iron ore for processes like gravity separation, magnetic separation, and flotation, which help increase the iron concentration in the ore.
The crusher and ball mill are critical machines in the iron ore processing chain. Crusher take on the first task of breaking down large raw iron ore into smaller pieces, while ball mills take over for finer grinding and size reduction. Together, these machines ensure that iron ore is efficiently processed, enabling industries to produce the high-quality iron and steel required for modern infrastructure and manufacturing.
By understanding the functions and capabilities of crusher and ball mills, mining and processing industries can optimize their operations, improving overall productivity and resource utilization.