Uzbekistan Iron Ore Crushing Line
Uzbekistan is home to a significant amount of iron ore reserves, making it a key player in the global iron ore industry. To efficiently process and beneficiate this valuable resource, iron ore crushing lines play a crucial role. These lines consist of a series of machines that work together to reduce the size of iron ore lumps into smaller particles, making them suitable for further processing and utilization.
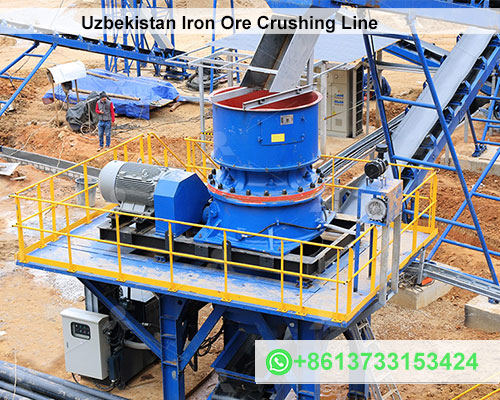
Components of an Uzbekistan Iron Ore Crushing Line
A typical Uzbekistan iron ore crushing line comprises the following components:
- Receiving and Feeding System: This system receives the raw iron ore from the mine and feeds it into the crushing process. It may include equipment like hoppers, conveyors, and feeders.
- Primary Crushing: The primary crusher breaks down the large iron ore lumps into smaller pieces, typically ranging from 200mm to 300mm in size. Jaw crusher, gyratory crusher, or impact crusher is commonly used for this purpose.
- Secondary Crushing: The secondary crusher further reduces the size of the iron ore particles, typically down to 50mm to 100mm. Cone crushers or impact crushers are often employed in this stage.
- Tertiary Crushing: Tertiary crushing, if necessary, further refines the iron ore particles to a size range of 25mm to 6mm. Cone crushers or hammer mills are commonly used for this purpose.
- Screening and Classification: Screening and classification equipment separates the crushed iron ore into different particle sizes based on their dimensions. This allows for the production of specific grades of iron ore products for various downstream applications.
- Conveying and Storage: Conveying systems transport the crushed and screened iron ore particles to storage silos or stockpiles. These systems ensure a continuous flow of material throughout the crushing line.
Factors Influencing the Design of Iron Ore Crushing Lines
Several factors influence the design of iron ore crushing lines in Uzbekistan, including:
- Feed Material Characteristics: The size, hardness, and abrasiveness of the raw iron ore feedstock significantly impact the selection of crushing equipment and the overall design of the line.
- Production Capacity: The desired production capacity of the crushing line determines the size and capacity of the individual crushing machines and other components.
- Product Size Requirements: The required size of the final iron ore product dictates the number of crushing stages and the specific equipment used in each stage.
- Energy Efficiency: Energy efficiency is a crucial consideration, as crushing operations consume a significant amount of power. Selecting energy-efficient equipment and optimizing the process flow can minimize energy consumption and reduce operating costs.
- Environmental Regulations: Environmental regulations governing dust emissions, noise levels, and water usage must be considered in the design and operation of iron ore crushing lines.
Uzbekistan’s Iron Ore Crushing Line Industry
Uzbekistan’s iron ore crushing line industry is characterized by the presence of both domestic and international suppliers. Domestic manufacturers cater to the needs of local mining companies, while international suppliers offer advanced technologies and expertise in designing and constructing large-scale crushing lines.
The industry is witnessing technological advancements, such as the adoption of high-pressure grinding rolls (HPGR) for finer grinding and the integration of automation and control systems for improved efficiency and safety.
As Uzbekistan’s iron ore production continues to grow, the demand for efficient and reliable iron ore crushing lines is expected to increase further. Domestic and international suppliers will need to stay at the forefront of technological innovation to meet the evolving needs of the Uzbekistani iron ore industry.