Flow chart extraction of iron crusher
The extraction of iron from its ore is a crucial industrial process, particularly in the steel-making industry. It involves multiple stages, starting from mining to beneficiation and ultimately refining into usable metal. Among these stages, crushing plays a pivotal role, as it reduces the raw material size, enabling the efficient extraction of iron. In this article, we will explore the flow chart for the extraction of iron, with a focus on the crushing stage, and how the overall process is organized to maximize efficiency.
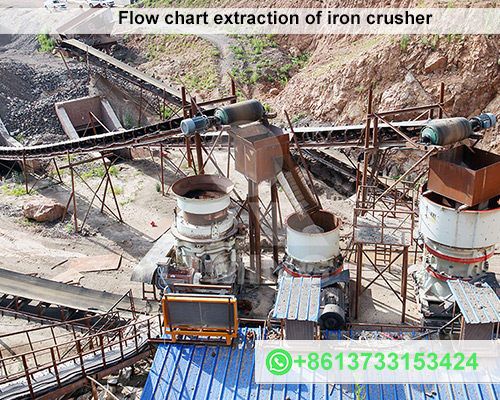
Overview of Iron Extraction Process
Before diving into the flow chart, it’s important to understand the broad stages of iron extraction:
- Mining: Iron ore is extracted from the ground using open-pit or underground mining techniques.
- Crushing and Screening: After extraction, the raw iron ore undergoes size reduction through crushing and is screened for further processing.
- Concentration and Beneficiation: The crushed ore is concentrated to remove impurities through methods such as magnetic separation or flotation.
- Pelletizing or Sintering: The concentrated iron ore is transformed into pellets or sinter to prepare it for smelting in blast furnaces.
- Smelting: The final step involves reducing the iron ore in a blast furnace to produce molten iron, which can then be refined into steel.
Step-by-Step Flow Chart of Iron Ore Crushing Process
The crushing stage is one of the initial stages in the iron extraction process, serving to reduce the large iron ore lumps into smaller particles, making subsequent processing steps easier. Here’s how the process typically flows:
1. Raw Material Feeding
- The raw iron ore, often in the form of large boulders or chunks, is transported from the mine to the crushing plant.
- A vibrating feeder or conveyor belt is commonly used to deliver the ore to the crusher, ensuring a consistent flow of material.
2. Primary Crushing
- In this step, the large iron ore pieces are fed into a jaw crusher or gyratory crusher, which exerts mechanical pressure to break the material into smaller pieces.
- The aim is to reduce the size of the ore from large boulders (sometimes more than 1 meter in diameter) to pieces typically measuring between 10-30 cm.
- Jaw crusher is frequently used due to their robust nature and high capacity.
3. Secondary Crushing
- After the initial crushing, the iron ore is further processed in secondary crusher, typically cone crusher or impact crusher.
- The goal here is to reduce the ore to a finer size, around 2-10 cm. Cone crusher is preferred for this stage due to their ability to handle harder ores like iron, and the finer output size they provide.
4. Screening
- Once the ore has been crushed, it is passed through a vibrating screen or other screening equipment to separate it into various size fractions.
- Larger particles are sent back to the crusher for further reduction, while smaller particles move on to the next stage of processing.
5. Tertiary Crushing (if necessary)
- If the secondary crushing does not reduce the ore to the required fine size, a tertiary crushing step may be added. This stage often employs high-efficiency crusher, such as high-pressure grinding rolls (HPGR) or vertical shaft impactors (VSI), to achieve very fine granulation.
6. Conveying and Stockpiling
- The finely crushed ore is conveyed through belt conveyors to stockpiles or further stages of processing.
- During this stage, proper blending and homogenization of the crushed material can take place, ensuring a uniform feed for the downstream beneficiation process.
Importance of Crushing in Iron Extraction
The crushing stage is critical in the iron extraction process for several reasons:
- Increased Surface Area: Crushing the iron ore increases the surface area available for the subsequent concentration processes like magnetic separation, making the separation more efficient.
- Efficiency in Transportation and Processing: Smaller particles are easier to transport and feed into further processing steps, reducing overall energy consumption.
- Optimal Liberation: By breaking down the iron ore, the valuable iron minerals are liberated from the surrounding impurities, which enhances the effectiveness of beneficiation methods like magnetic separation or froth flotation.
Considerations for Effective Crushing
To ensure that the crushing process is efficient and yields high-quality iron concentrate, several factors need to be taken into account:
- Crusher Type: Selecting the right type of crusher based on the material hardness and desired output size.
- Feed Rate: Regulating the feed rate to prevent overloading the crusher and ensure consistent material flow.
- Crusher Maintenance: Regular maintenance and monitoring of crusher to prevent wear and tear, reducing the risk of breakdowns.
The flow chart of iron extraction with a focus on the crushing process illustrates the step-by-step breakdown of how iron ore is reduced in size for further processing. From initial raw material feeding through primary and secondary crushing to final screening, each stage plays an essential role in preparing the ore for beneficiation. By optimizing the crushing stage, operators can improve the efficiency and overall effectiveness of the iron extraction process, ensuring the production of high-quality metal at reduced costs.