Cone Crusher Diagram for Manganese Ore Mineral Processing
Manganese ore, known for its hardness (5-6 Mohs) and abrasive nature, demands robust crushing solutions. Cone crusher is widely used in mineral processing for their ability to deliver uniform particle size and handle high-capacity operations. This article breaks down the cone crusher diagram, its role in manganese ore processing, and best practices for maximizing productivity.
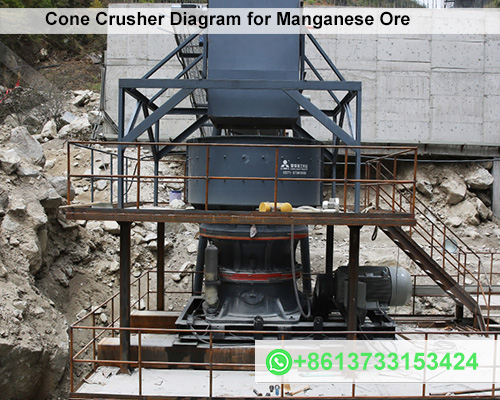
Why Use Cone Crusher for Manganese Ore?
Cone crusher excel in secondary and tertiary crushing stages, offering:
- High Reduction Ratio: Reduces ore from 100-250 mm to ≤25 mm.
- Wear Resistance: Manganese steel liners withstand abrasive materials.
- Energy Efficiency: 20-30% lower energy consumption vs. jaw crusher for similar outputs.
Cone Crusher Diagram: Key Components Explained
Below is a breakdown of a standard cone crusher’s structure in manganese ore processing:
- Feed Hopper
Directs raw manganese ore into the crushing chamber. - Eccentric Assembly
Rotates the mantle to create compressive force against the concave. - Crushing Chamber
- Mantle: Movable manganese steel cone.
- Concave: Fixed outer liner, designed for optimal ore compression.
- Hydraulic System
Adjusts the crusher’s closed-side setting (CSS) to control output size. - Discharge Conveyor
Transports crushed ore to screening or further processing.
Figure 1: Schematic diagram of a cone crusher in manganese ore processing.
How Cone Crusher Process Manganese Ore
- Primary Crushing (Optional):
Jaw crusher reduce ore to ≤200 mm. - Secondary Crushing:
Cone crusher further break down ore to 25-50 mm. - Tertiary Crushing:
Fine-tuning to ≤10 mm for leaching or smelting.
Critical Design Features for Manganese Ore:
- Anti-Spin Mechanism: Prevents uneven wear on the mantle.
- Tramp Release System: Protects the crusher from uncrushable materials.
Top 3 Cone Crusher Models for Manganese Ore
Model | Capacity (t/h) | Key Feature |
---|---|---|
Liming HPT300 | 200-350 | Patented Hydroset™ system for CSS adjustment. |
Liming HPT200 | 150-250 | Multi-Action Technology for 10% higher output. |
Liming HST160 | 120-220 | Hybrid diesel/electric power option. |
4 Maintenance Tips to Reduce Downtime
- Liner Inspection
Replace concave and mantle when wear exceeds 20% thickness. - Lubrication
Use high-viscosity oil (ISO VG 320) for high-temperature operations. - Belt Tensioning
Check drive belts monthly to prevent slippage. - Sensor Integration
Install IoT wear sensors for real-time monitoring.
Case Study: Improving Yield in South Africa
A manganese mine in the Kalahari Basin upgraded to a Liming HPT300 cone crusher, achieving:
- 15% increase in throughput (from 180 t/h to 207 t/h).
- 30% longer liner lifespan due to optimized CSS settings.
How to Choose the Right Cone Crusher
Consider these factors:
- Ore Characteristics: High abrasiveness requires ultra-high manganese steel (UHMS) liners.
- Capacity Needs: Match crusher size to plant output (e.g., 200 t/h for mid-sized mines).
- Automation: Opt for models with ASRi™ or similar control systems for consistent product size.
Conclusion
Understanding the cone crusher diagram for manganese ore mineral processing helps operators optimize crushing efficiency and reduce operational costs. Prioritize crusher with adaptive hydraulic systems and wear-resistant materials. By understanding the cone crusher diagram and its application in manganese ore mineral processing, companies can optimize their operations and achieve higher yields. Whether for industrial or smelting purposes, cone crusher remain a vital component in the production of high-quality manganese products.