Manganese Ore Crushing Production Process
Manganese is widely distributed in nature, and almost all ores and silicate rocks contain manganese. The most common manganese ores are water-free and hydrated manganese oxides and manganese carbonates. There are 150 known manganese minerals, but only 5-6 of them are ideal for manganese enrichment and have economic value. The more important and valuable ones are rhodochrosite and pyrolusite, and there are also manganite, braunite, hausmannite, and rhodonite. The manganese content in these minerals can reach about 50-70%, making them important industrial minerals of manganese.
Manganese ore processing production process
The production process of manganese ore processing mainly includes three processes: crushing, grinding, and beneficiation. In the crushing process, the three-stage closed-circuit crushing is a modern and suitable method for crushing high-hardness manganese ore, which can complete the crushing and partial dissociation of the ore, thereby improving the subsequent grinding efficiency. In the grinding process, the two-stage closed grinding is an efficient grinding process that can make the manganese ore more fully ground. In the beneficiation process, the representative successful new processes in recent years mainly include: “stage grinding, weak magnetic separation-reverse flotation process”, “full magnetic separation and selection process”, and “ultra-fine crushing-wet magnetic separation tailings process”.
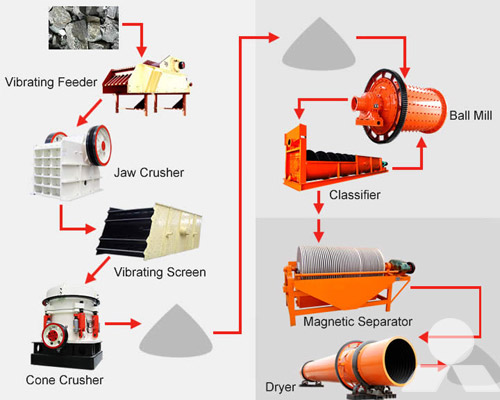
1: Crushing and screening
Large pieces of manganese ore are evenly sent to the jaw crusher or mobile jaw crushing station (primary crushing) by the vibrating feeder through the silo for primary crushing;
The coarsely crushed manganese ore is screened by a vibrating screen, and sent to a single-cylinder hydraulic cone crusher (secondary crushing) by a belt conveyor for secondary crushing;
The manganese ore material after secondary crushing is sent to the multi-cylinder hydraulic cone crusher for fine crushing.
Jaw crushers are mainly used for medium-sized crushing of ores and large materials, and can crush materials with a compressive strength of up to 320Mpa, and are divided into coarse crushing and fine crushing. Liming Heavy Industry has PE and PEW series jaw crushers with complete product specifications, a feed size of 125mm to 1020mm, and a single machine output up to 800t/h, making it an ideal choice for primary crushing equipment. The structure is sturdy and the performance is stable: using world advanced technology, Baosteel high-quality steel, Timken bearings from the United States, heavy-duty eccentric shaft, finite element analysis technology, making its structure sturdy and performance stable, and long-term operation; high crushing ratio and high output: using heavy-duty trough wheels and flywheels, optimized jaw plates, making the crushing force greater; the “V” design makes its feed port consistent with the actual situation, the crushing chamber is deep and there is no dead zone, and the output is higher; easy to operate and energy-saving: hydraulic lubrication, wedge adjustment makes it more convenient and flexible to operate, lubrication is more convenient, and the single machine saves 15% to 30% of energy, and the system saves twice as much.
HST series single-cylinder hydraulic cone crusher is widely used in the medium and fine crushing process of metal mines such as iron ore, gold ore,manganese ore, and copper ore. Liming Heavy Industry’s HST single-cylinder hydraulic cone crusher is a high-efficiency crusher designed based on American advanced technology and the performance of high-quality materials in the industry. The structure is solid and the performance is stable: it uses an integrated frame casting, heavy-duty central shaft, and both ends of the main shaft are supported, which has strong load-bearing capacity and great crushing force. It adopts advanced technology and imported Timken bearings from the United States, which makes the operation stable and has a long service life. It has automated control and is easy to operate: it uses PCL touch screen operation and hydraulic adjustment discharge mode, which makes the adjustment of the discharge port convenient, maintenance easier, and the replacement of the fixed cone more convenient and efficient, reducing downtime. It has integrated thin oil lubrication: it uses an integrated thin oil lubrication system, which is more efficient in lubrication and saves lubricating oil. It uses a wind cooling system to cool the thin oil, overcomes environmental limitations, and makes the overall process more stable and efficient.
HPT series hydraulic cone crusher is a new generation of high-efficiency hydraulic cone crusher launched based on nearly thirty years of crusher R&D experience, combined with advanced technology at home and abroad, and several generations of product development and application. Based on the traditional multi-cylinder hydraulic cone crusher’s structure of fixed main shaft and eccentric sleeve rotating around the main shaft and laminated crushing principle, HPT series has made breakthrough optimizations in equipment structure, significantly improving the equipment’s performance and crushing capacity. The supporting hydraulic lubrication system ensures reliable equipment operation, and the operation control is more intelligent and user-friendly. The upgraded structure is more efficient: based on the unique structure of the fixed main shaft and eccentric sleeve rotating around the main shaft, the transmission rotating parts and lubrication sealing structure design have been further optimized, the equipment’s load-bearing capacity is strong, the installed power is very large in the same industry, the volume is small, the efficiency is high, and the noise is low.
Tire-type mobile crushing station is widely used in the crushing process of mines. It can overcome the obstacles of crushing site, environment, complicated basic configuration, and complicated logistics brought by the customers’ crushing operations, providing customers with high-efficiency and low-cost project hardware facilities. Liming Heavy Industry’s tire-type mobile crushing station has been successfully applied in domestic and foreign mining crushing projects, playing a huge role. It is flexible and reduces costs: it is equipped with vehicle traction, compact structure, stable and sturdy, suitable for working in harsh mountain environments, and can crush materials on-site, eliminating the intermediate link of transporting materials away from the work site for crushing, greatly reducing the transportation cost of materials. It is adaptable and can be customized as needed: the crushing station can be equipped with an independent generator set, and even if the local power grid cannot be used, the machine can still operate normally. At the same time, our company can specially customize the mobile crushing station according to the customer’s site, material, particle size, and other requirements.
2: Grinding
The 0-12mm manganese powder screened by the vibrating screen is evenly fed into the ball mill for grinding, and screened by the spiral classifier. The material that does not meet the requirements is sent back to the ball mill for further grinding.
Ball mill is a commonly used grinding equipment in a dressing plant. It is suitable for grinding iron ore, manganese ore, manganese ore, tungsten ore, copper ore and other minerals. It is used to grind the ore below 0.075mm to make the useful minerals fully monomer Dissociation for subsequent work sorting. According to different ore discharge methods, it can be divided into grid type ball mill and overflow type ball mill. Its grinding method can be divided into dry and wet grinding methods.
The spiral classifier, also known as the classifier, is one of the beneficiation equipment. The spiral classifier uses the principle that the solid particles have different specific gravity and therefore precipitate at different speeds in the liquid to perform mechanical classification. It can classify the powder from the mill according to the filtering, and then use the spiral blade to rotate into the mill feeding port for coarse material, and discharge the filtered fine material from the overflow pipe.
3: Flotation
Send the manganese powder that meets the mineral processing requirements into the magnetic separator for strong magnetic separation and magnetic separation to remove impurities;
Magnetic separator is a device that uses an appropriate magnetic field strength to select iron powder from powdery particles. Magnetic separators are widely used in ore dressing and are suitable for wet magnetic separation of materials such as magnetite, magnetic pyrite, roasted ore, and titanium iron ore with a particle size of less than 3mm. They are also used for iron removal operations of materials such as coal, non-metallic minerals, and building materials. They are one of the widely used and versatile models in the industry.
High-intensity magnetic separator is a device that uses a high-intensity magnetic field strength to screen iron powder from powdery particles. High-intensity magnetic separators are widely used in metal ore dressing with iron symbiosis, and are suitable for wet magnetic separation of materials such as magnetite, magnetic pyrite, roasted ore, and titanium iron ore with a particle size of less than 3mm. They are also used for iron removal operations of materials such as coal, non-metallic minerals, and building materials. They are one of the widely used and versatile models in the industry.
4: Drying
The obtained manganese powder is sent to the drying machine for drying to obtain manganese concentrate powder.
The drying machine is a commonly used equipment in mining beneficiation, including a rotating drum. The inner drum is driven by a belt and there is hot air around the drum to evaporate the moisture. The drying drum uses the principle of reversing rotation to achieve the effect of not entangling the dried materials, so that the moisture in the materials can be removed.