Specification for Static Crushing and Screening Equipment
Static crushing and screening equipment is a crucial component of the aggregate production process, transforming raw materials into usable products for construction, road building, and other applications. These systems are designed to operate in a fixed location, offering a robust and reliable solution for large-scale production.
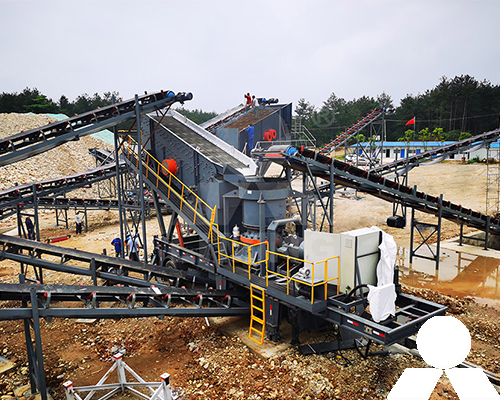
Crushing Equipment
Crushing equipment plays a primary role in reducing the size of feed material, typically from quarry rocks or boulders, into smaller particles. The selection of crushing equipment depends on the desired product size and material characteristics. Common types of static crushers include:
- Jaw Crusher: These crushers utilize two opposing jaws to break material into smaller pieces. They are suitable for primary crushing applications, handling large feed sizes.
- Gyratory Crusher: Similar to jaw crushers, gyratory crushers employ a rotating cone to reduce material size. They are known for their high capacity and efficiency in secondary and tertiary crushing stages.
- Cone Crusher: These crushers use a rotating cone against a concave liner to crush material. They are particularly effective in producing finer particles and are commonly used in secondary and tertiary crushing stages.
Screening Equipment
Screening equipment separates crushed material into different particle sizes based on their dimensions. Vibrating screens are the most common type of static screening equipment, utilizing a vibrating motion to pass material through various sieve openings. Key factors to consider when selecting a screen include:
- Screen Size: The size of the screen determines the maximum feed size and the range of particle sizes it can separate.
- Number of Decks: Multi-deck screens allow for simultaneous classification of material into multiple product sizes.
- Screen Media: The type of screen media, such as woven wire mesh or perforated plates, influences the separation efficiency and product quality.
Specification Considerations
When specifying static crushing and screening equipment, several factors must be carefully considered to ensure optimal performance and product quality:
- Feed Material Characteristics: The type, hardness, and size of the feed material significantly impact the selection of crushing and screening equipment.
- Desired Product Size Distribution: The target particle sizes and the required proportions of each size dictate the arrangement and configuration of crushing and screening stages.
- Production Capacity: The desired production rate determines the size and capacity of the equipment required to meet throughput demands.
- Power Requirements: The power consumption of crushing and screening equipment is a significant operational cost factor, and energy-efficient options should be considered.
- Maintenance Considerations: Ease of access for maintenance and the availability of spare parts are crucial for minimizing downtime and ensuring long-term operational efficiency.
Static crushing and screening equipment plays a vital role in the aggregate production process, transforming raw materials into valuable construction materials. By carefully considering the feed material characteristics, desired product size distribution, production capacity, power requirements, and maintenance considerations, engineers can select the most appropriate equipment for specific applications, ensuring efficient and productive operation.