Slag Crusher for Steel Plant Recycling
Introduction to Steel Slag Recycling
Steel production generates massive amounts of slag, a byproduct that traditionally ends up in landfills. However, modern slag crusher transform this waste into valuable resources like construction aggregates, road base materials, and even cement additives. For steel plants aiming to reduce environmental impact and unlock new revenue streams, investing in a slag crusher for steel plant recycling is a game-changer. This article explores the technology, benefits, and best practices for slag processing.
What is Steel Slag?
Steel slag is a hard, dense material formed during steelmaking processes like blast furnace (BF) or electric arc furnace (EAF) operations. It contains minerals such as calcium, iron, and silica, making it ideal for recycling into construction and industrial applications.
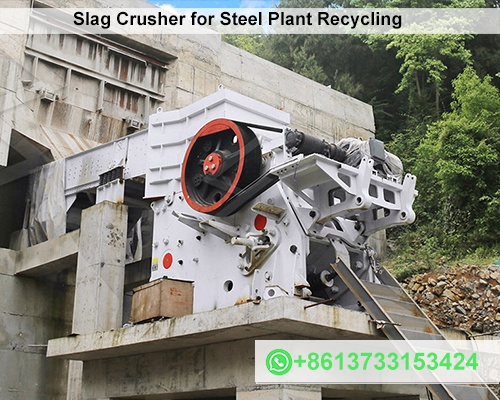
How a Slag Crusher Works
A slag crusher mechanically breaks down large chunks of slag into smaller, uniform particles. The process typically involves:
- Primary Crushing:Jaw crusher reduce slag chunks to 150–300 mm.
- Secondary Crushing:Cone or impact crusher further refine the material to 10–50 mm.
- Screening:Vibrating screens separate particles by size (e.g., 0–5 mm, 5–20 mm).
- Magnetic Separation:Removes residual metal fragments for higher-purity slag aggregates.
Types of Slag Crusher for Steel Plants
1. Jaw Crusher
- Best for:Primary crushing of large, hard slag blocks.
- Features:High compressive strength, simple maintenance.
- Model Example:Liming C6X Jaw Crusher (Capacity:160–1,500 TPH).
2. Impact Crusher
- Best for:Producing cubical-shaped aggregates for concrete.
- Features:Adjustable rotor speed, low dust emission.
- Model Example:Liming CI5X Impact Crusher (Capacity:250–2,000 TPH).
3. Cone Crusher
- Best for:Secondary/Tertiary crushing of abrasive slag.
- Features:Hydraulic adjustment, automatic overload protection.
- Model Example:Liming HPT Multi-Cylinder Hydraulic Cone Crusher.
4. Mobile Slag Crusher
- Best for:On-site processing in limited spaces.
- Features:Diesel-electric hybrid power, integrated screening.
Benefits of Using a Slag Crusher in Steel Plants
- Waste Reduction:Recycle up to 100% of steel slag, eliminating landfill costs.
- Revenue Generation:Sell processed slag as aggregates ($10–30/ton) or cement additives.
- Sustainability:Reduce CO2 emissions by 40% compared to virgin material production.
- Compliance:Meet environmental regulations (e.g., EU Waste Framework Directive).
Applications of Processed Steel Slag
- Construction:Substitute for natural gravel in concrete and asphalt.
- Railway Ballast:Durable, drainage-friendly material for rail tracks.
- Agriculture:Soil conditioner to neutralize acidic soils.
- Industrial:Raw material for glass manufacturing and abrasives.
How to Choose the Right Slag Crusher
- Slag Properties:Analyze hardness (Mohs 6–7), moisture, and metal content.
- Capacity Needs:Match crusher output (TPH) to your slag production volume.
- Mobility:Opt for mobile crusher if space is limited or slag piles are dispersed.
- After-Sales Support:Choose suppliers offering spare parts and maintenance training.
Case Study:Slag Recycling Success in Germany
A German steel plant integrated a Liming Mobile Impact Crusher (Model:K3S216) to process 500 TPD of EAF slag. Results:
- 90% Landfill Diversion:Saved €200,000 annually in waste fees.
- New Revenue:Sold slag aggregates to local road builders, earning €1.2M/year.
- Energy Savings:Hybrid power reduced fuel costs by 25%.
Environmental and Safety Considerations
- Dust Control:Use water sprays or enclosed crushing systems.
- Noise Reduction:Soundproof enclosures for urban plants.
- Worker Safety:Automated feeding systems minimize manual handling.
Conclusion
A slag crusher for steel plant recycling is no longer optional—it’s a strategic necessity for sustainable, profitable steel production. By converting waste into high-demand materials, steel plants can cut costs, comply with regulations, and contribute to a circular economy.