Brazil Vertical shaft impact crusher
Vertical Shaft Impact Crusher (VSI crusher) is a type of crusher that utilizes a high-speed rotor with a crushing chamber that’s designed to throw the materials against hard and abrasive surfaces. This crushing process is carried out by rock-on-rock action, as the rocks are accelerated by the rotor and impacted against stationary anvils or curtains to break them down into smaller pieces.
Vertical Shaft Impact Crushers are commonly used in the aggregate, mining, and construction industries for producing artificial sand, crushed sand, and shaping aggregates. They are also used for reducing the size of rocks and minerals in various applications.
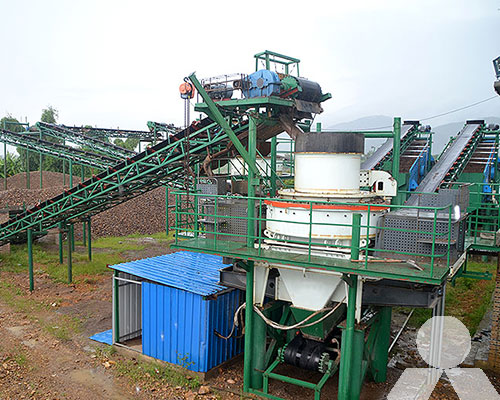
Here’s how a typical Vertical Shaft Impact Crusher works:
- Feed Material: Rocks or other materials are fed into the top of the crusher through a hopper or a tube.
- Rotor and Crushing Chamber: The rotor of the crusher spins at a high speed. The rocks entering the rotor are accelerated and thrown outward against the stationary anvils or curtains that line the crushing chamber. This impact causes the rocks to break and fragment.
- Crushing Action: The energy from the impact causes the rocks to undergo significant impact and abrasion, resulting in the reduction of their size. Depending on the specific design of the crusher, the rocks can be crushed into fine particles or even smaller sizes.
- Particle Shaping: In addition to crushing, VSI crushers are known for their ability to shape the particles as they are crushed. The high-speed impact causes the rocks to fracture along their natural lines, creating a more cubical and well-graded end product, especially when producing artificial sand.
- Discharge: The crushed and shaped particles are then discharged from the bottom of the crusher.
- Adjustability: Many VSI crushers come with adjustable components that allow operators to control the size and shape of the final product. This adjustability can be valuable in producing materials for specific applications.
Vertical Shaft Impact Crushers offer advantages such as high crushing efficiency, versatility in material types, and the ability to produce well-shaped and consistent end products. However, they can be sensitive to feed gradation and require proper maintenance to ensure optimal performance.