Artificial Aggregate Processing Plant Design and Calculation
Designing an artificial aggregate processing plant involves several steps and considerations to ensure efficiency, productivity, and safety. Here’s a general overview of the process and calculations involved:
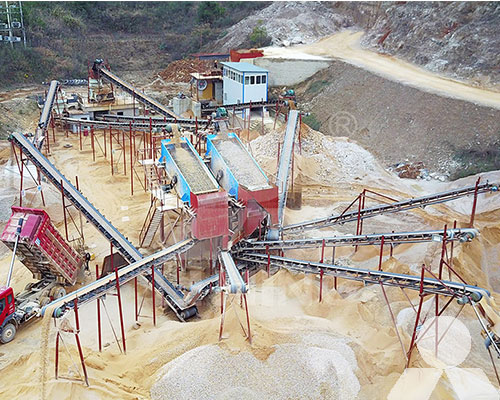
1. Site Assessment and Planning:
- Determine the location of the plant considering factors like proximity to raw material sources, transportation routes, and environmental regulations.
- Assess the available space for the plant layout and consider future expansion.
2. Raw Material Analysis:
- Analyze the properties of the raw materials (e.g., rocks, minerals) to determine their suitability for aggregate production.
- Consider factors like hardness, abrasiveness, moisture content, and gradation of the raw materials.
3. Plant Layout:
- Design a layout that optimizes the flow of materials and processes, minimizing bottlenecks and optimizing efficiency.
- Allocate space for equipment such as crushers, screens, conveyors, storage bins, and control rooms.
4. Equipment Selection and Sizing:
- Choose appropriate equipment based on the properties of the raw materials and desired output specifications.
- Size crushers and screens to achieve the desired aggregate sizes and production rates.
5. Process Flow:
- Develop a detailed process flow diagram that outlines the sequence of operations from raw material intake to final aggregate products.
- Include steps such as crushing, screening, washing (if needed), and stockpiling.
6. Material Handling:
- Calculate conveyor capacities and speeds to ensure efficient material transport between different stages of the process.
7. Crushing and Screening:
- Determine the type of crushers (e.g., jaw crushers, cone crushers) and screens (e.g., vibrating screens, inclined screens) based on the material characteristics and required final products.
- Calculate crusher settings and screen sizes to achieve the desired aggregate gradation.
8. Washing (if applicable):
- Design a washing system if the raw materials contain excessive fines or impurities.
- Consider factors like water availability, settling ponds, and environmental regulations.
9. Stockpiling and Storage:
- Calculate the required storage capacity for different aggregate products.
- Design stockpiles for easy access, proper drainage, and minimal segregation.
10. Utilities and Infrastructure:
- Plan for power supply, water sources, and waste disposal systems.
- Consider safety features, such as dust suppression and noise reduction measures.
11. Environmental Considerations:
- Ensure compliance with local environmental regulations and obtain necessary permits.
- Implement dust control, noise reduction, and water management measures.
12. Safety Measures:
- Design the plant layout and workflows with safety in mind, including proper signage, emergency exits, and protective barriers.
- Provide proper training for employees operating the equipment.
13. Cost Estimation:
- Calculate the initial investment costs, including equipment, infrastructure, and construction.
- Estimate ongoing operational costs, including labor, energy, maintenance, and raw materials.
14. Continuous Improvement:
- Design the plant with flexibility in mind to accommodate future changes in demand or technology.
- Plan for regular maintenance and upgrades to optimize performance and efficiency.
Remember that specific calculations and designs will vary depending on the scale of the plant, the types of raw materials, local regulations, and other factors. It’s essential to collaborate with experienced engineers, geologists, and industry experts during the design process to ensure a successful and efficient aggregate processing plant.