150th-200th Granite Crushing Plant
Granite crushing plants are essential components of the construction industry, transforming large, quarried granite rocks into usable aggregate materials for various applications. These plants typically range in capacity from a few tons per hour (TPH) to hundreds of TPH, with 150th-200th TPH plants falling into the mid-range category.
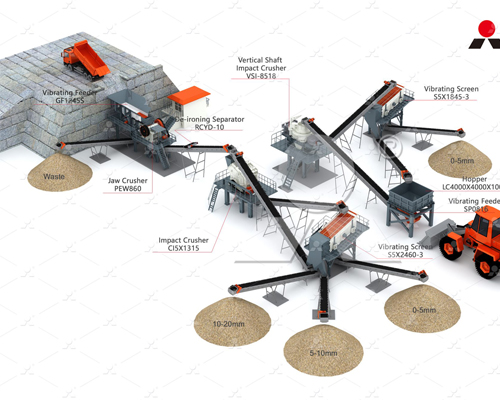
Key Components of a 150th-200th Granite Crushing Plant
A 150th-200th TPH granite crushing plant typically comprises several key components that work together to efficiently process the raw material:
- Feeders: These devices regulate the flow of granite rocks into the crushing process, ensuring a steady and manageable feed for the crusher.
- Primary crusher: These robust machines, often jaw crusher or gyratory crusher, break down the large granite rocks into smaller pieces, typically ranging from 6 inches to 3 inches in size.
- Secondary crusher: These crusher, such as cone crusher or impact crusher, further reduce the granite pieces to a more uniform size, usually between 1 inch and 2 inches.
- Tertiary crusher: In some cases, tertiary crusher may be employed to achieve even finer particle sizes, catering to specific application requirements.
- Vibrating Screens: These screens classify the crushed granite into different particle sizes, ensuring that the final product meets the desired specifications.
- Conveyors: Conveyors transport the crushed granite throughout the plant, from one stage to the next, and ultimately to storage or loading areas.
- Dust Collection Systems: These systems capture and control dust generated during the crushing process, maintaining a safe and environmentally friendly working environment.
Applications of Granite Products from a 150th-200th TPH Plant
Granite products processed by a 150th-200th TPH plant find diverse applications across various industries:
- Construction: Granite aggregates are widely used in concrete mixes, asphalt pavements, and road construction due to their exceptional strength, durability, and resistance to wear and tear.
- Landscaping: Granite gravel and crushed stone are popular choices for landscaping projects, providing attractive and durable walkways, driveways, and decorative accents.
- Railroad Construction: Granite ballast is essential for railroad tracks, ensuring stability and drainage, and minimizing track deformation under heavy train loads.
- Abrasive Blasting: Granite grit is used in abrasive blasting applications, such as surface cleaning and preparation for painting or coating.
- Water Filtration: Crushed granite serves as a filtration medium in water treatment plants, removing impurities and ensuring clean drinking water.
Factors to Consider When Selecting a 150th-200th TPH Granite Crushing Plant
Several factors should be considered when selecting a 150th-200th TPH granite crushing plant:
- Production Capacity: The plant’s capacity should align with the anticipated production requirements and the volume of granite to be processed.
- Material Characteristics: The plant’s design should suit the specific characteristics of the granite being processed, such as hardness, grain size, and abrasiveness.
- Desired Product Sizes: The plant’s configuration should be able to produce the desired range of granite particle sizes for the intended applications.
- Environmental Regulations: The plant should comply with local environmental regulations regarding dust emissions and noise levels.
- Reliability and Durability: The plant should be constructed from high-quality materials and components to ensure long-term reliability and durability.
- After-Sales Support: The supplier should provide comprehensive after-sales support, including spare parts availability, maintenance services, and technical assistance.
Conclusion
150th-200th TPH granite crushing plants play a crucial role in the production of construction aggregates and other valuable granite products. By carefully selecting a plant that meets specific requirements and considering factors such as capacity, material compatibility, product size specifications, environmental compliance, reliability, and after-sales support, operators can ensure efficient, productive, and sustainable granite processing operations.