Jaw Stone Crusher for Granite
Granite is one of the hardest and most durable natural stones used in various industries, including construction, flooring, and countertops. Extracting granite from quarries and processing it into usable sizes requires specialized equipment. Among the key machines used for this purpose is the jaw stone crusher. This article explores the role of jaw crushers in granite processing, their types, working principles, benefits, and key considerations when choosing the right machine for your granite crushing needs.
What is a Jaw Stone Crusher?
A jaw stone crusher is a primary crushing machine widely used in the mining, quarrying, and construction industries. It is particularly effective for reducing large blocks of hard material like granite into smaller, more manageable pieces. The crusher consists of two jaws, one stationary and one movable, which form a V-shaped cavity. As material enters the crusher, the movable jaw compresses it against the stationary jaw, breaking it into smaller pieces.
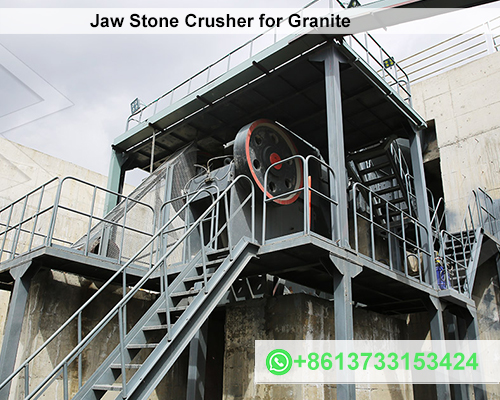
Types of Jaw Crushers for Granite
There are various types of jaw crushers used for granite processing, each designed to handle different sizes and hardness levels of material. The primary distinctions are:
- Single Toggle Jaw Crusher:
- In this design, the movable jaw is supported on a single pivot point.
- It has a simple structure and is often preferred for smaller scale operations and less abrasive materials.
- While effective for crushing granite, single toggle jaw crushers may not be as durable or efficient for highly abrasive or larger stones.
- Double Toggle Jaw Crusher:
- This design features two toggle plates, which provide more crushing force.
- It is typically more robust and capable of handling larger, harder materials like granite.
- The double toggle mechanism allows for a more uniform particle size distribution and is more durable, especially in heavy-duty applications.
- European Type Jaw Crusher:
- A more advanced version of the jaw crusher, incorporating modern design elements for better efficiency and energy savings.
- These crushers often feature reinforced frames and improved bearings, offering higher performance when crushing hard granite.
- Mobile Jaw Crusher:
- A mobile unit mounted on tracks or wheels, designed for flexibility and easy transportation between job sites.
- Particularly useful in large-scale quarries where granite extraction and processing take place on-site.
Working Principle of a Jaw Crusher
The basic working principle of a jaw stone crusher is relatively simple, but highly effective:
- Feeding: Large granite blocks are fed into the jaw crusher’s feed opening, which is typically equipped with a vibrating feeder for even distribution of the material.
- Compression: As the movable jaw swings in a circular motion, it compresses the granite against the fixed jaw.
- Crushing: The granite is progressively reduced in size as it passes through the narrow gap between the jaws.
- Discharge: Once the granite is sufficiently broken down into smaller pieces, it is discharged from the bottom of the machine.
Benefits of Using a Jaw Stone Crusher for Granite
- High Efficiency: Jaw crushers are designed to crush large chunks of granite quickly, ensuring efficient material processing. They provide a consistent output, reducing downtime during operation.
- Durability: Granite is a very hard material, and jaw crushers built for granite processing are specifically designed with durable components like high-strength steel plates, reinforced bearings, and robust frames to withstand the abrasive nature of the stone.
- Cost-Effectiveness: Jaw crushers have a simple design, making them relatively affordable compared to other types of crushers. They also have lower operating costs and require less maintenance.
- Versatility: Jaw crushers can be used to process a variety of other hard materials, which makes them versatile for various applications, including recycling, mining, and aggregate production.
- Particle Size Control: Jaw crushers offer precise control over the size of the final product, ensuring that the material meets the specific requirements of the downstream processing stages.
Key Considerations When Choosing a Jaw Crusher for Granite
- Capacity:
- It’s essential to choose a jaw crusher with a capacity that matches the scale of your operation. If you’re processing a high volume of granite, a larger capacity crusher will be necessary to maintain productivity.
- Jaw Crusher Size:
- The size of the jaw opening and the gap between the jaws will determine the size of the feed material and the final product. Granite blocks vary in size, so it’s important to select a crusher with a suitable size for your needs.
- Material Hardness:
- Granite is extremely hard and abrasive. Ensure the crusher is made from durable materials, such as high manganese steel, to handle the hardness of granite without significant wear.
- Automation Features:
- Some modern jaw crushers come with automated systems that allow for easier control of the crushing process, improving efficiency and reducing manual intervention.
- Energy Efficiency:
- Crushers that consume less power while maintaining high output can significantly reduce operational costs, especially in large-scale granite quarries.
- Maintenance and Spare Parts:
- Look for machines with accessible parts for easy maintenance. Some manufacturers offer extended warranties and spare parts availability to ensure long-term performance.
Common Applications of Jaw Crushers in Granite Processing
- Quarrying: In granite quarries, jaw crushers are used to break down massive granite blocks into smaller sizes for further processing or sale.
- Aggregate Production: Crushed granite is often used as an aggregate material for construction projects, such as roads, pavements, and buildings.
- Granite Recycling: Jaw crushers are also used in the recycling of granite from old structures and surfaces, breaking it down into smaller pieces for reuse.
- Stone Polishing: After primary crushing, the granite may undergo additional processing steps such as polishing or cutting, where uniform particle sizes are crucial.
Conclusion
A jaw stone crusher is an essential piece of machinery in the granite industry, providing a reliable and cost-effective method for breaking down hard stone into smaller, usable sizes. By understanding the different types of jaw crushers available, their working principles, and key considerations, you can make an informed decision on the best equipment for your specific granite processing needs. Whether you’re in the quarrying business, producing aggregates, or recycling old granite, investing in a high-quality jaw crusher can significantly enhance your production efficiency and output quality.