Granite Quarry Crushing Plant Layout
Granite quarry crushing plants play a pivotal role in the production of high-quality aggregate for various construction purposes. The layout of such plants is crucial to ensure efficient operations, minimize costs, and maximize output. This article explores the essential components, considerations, and best practices for designing an optimal granite quarry crushing plant.
Understanding Granite Quarry Crushing
Granite is a hard, durable natural stone widely used in construction. Crushing this material requires specialized equipment and a systematic approach to ensure that the desired product size and quality are achieved. A well-designed layout ensures smooth workflow and reduced downtime.
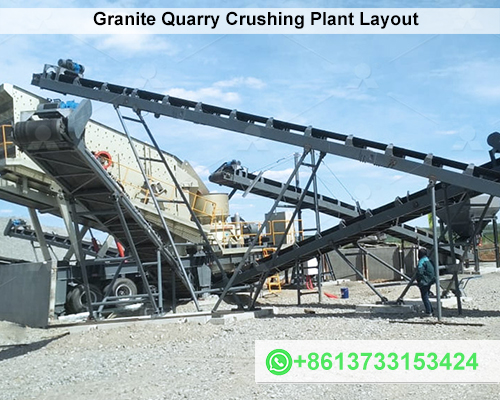
Key Components of a Granite Quarry Crushing Plant
- Primary Crushing Station
- Equipment: Jaw Crusher or Gyratory Crusher
- Purpose: The primary crusher reduces large granite blocks (up to 1.5 meters in diameter) into manageable sizes.
- Location: Positioned near the quarry face to minimize haulage costs.
- Secondary Crushing Station
- Equipment: Cone Crusher or Impact Crusher
- Purpose: Further reduces the size of material from the primary crusher to meet the specifications for aggregate production.
- Screening Units
- Equipment: Vibrating Screens
- Purpose: Classifies crushed material into different sizes and grades for specific applications.
- Tertiary Crushing (Optional)
- Equipment: High-speed Cone Crusher or Vertical Shaft Impact Crusher (VSIs)
- Purpose: Produces fine aggregates or specific particle shapes for specialized applications.
- Conveyors and Feeders
- Purpose: Ensure smooth material flow between crushing stages and storage areas. Proper conveyor design reduces spillage and maintenance.
- Storage and Loading
- Purpose: Stockpiles finished products for shipment or further processing. Silos or hoppers may be included for efficient loading.
Layout Considerations
- Flow Optimization
- Ensure a logical flow of materials from the primary crusher to secondary/tertiary stages and final stockpiles.
- Minimize crossovers to reduce congestion and potential delays.
- Space Utilization
- Compact designs save land area while allowing easy access for maintenance and inspection.
- Proximity to Quarry Face
- Placing the primary crusher close to the excavation site minimizes hauling costs.
- Conveyor systems can replace trucks for more sustainable and cost-effective transport.
- Environmental Compliance
- Incorporate dust suppression systems, noise reduction measures, and wastewater treatment facilities.
- Ensure compliance with local environmental regulations.
- Safety
- Design for easy access to equipment for repairs and regular inspections.
- Include emergency stop systems, proper lighting, and barriers around moving parts.
- Scalability
- Design with future expansion in mind.
- Modular layouts allow for the addition of equipment as demand grows.
Best Practices for Granite Crushing Plant Layout
- Automation: Use automation to monitor and control crushing processes, improving efficiency and reducing human error.
- Redundancy: Include backup systems for critical components like power supplies and crusher.
- Energy Efficiency: Opt for energy-efficient equipment to reduce operating costs and environmental impact.
- Regular Maintenance: Design with ease of maintenance in mind, ensuring minimal downtime.
Conclusion
An efficient granite quarry crushing plant layout ensures seamless operations, cost savings, and high-quality output. The integration of advanced technologies, careful planning, and environmental considerations will yield a setup that meets both operational and regulatory demands. Whether you’re setting up a new plant or upgrading an existing one, adhering to these principles will enhance productivity and profitability in the long run.