Granite Primary Crushing Equipment
Granite, one of the most popular and durable natural stones, is widely used in construction, architecture, and various other industries. Whether it’s for countertops, flooring, or building materials, granite’s strength and aesthetic appeal make it a preferred choice. However, before granite can be used in these applications, it must undergo a series of crushing and processing stages to transform it from large, rough blocks into usable aggregates and fine materials. The first step in this process is primary crushing, where large granite rocks are reduced in size for further processing.
In this article, we will explore the essential equipment used in the primary crushing of granite, which is a critical stage in granite processing.
What is Primary Crushing?
Primary crushing is the first step in the granite processing cycle. During this stage, large boulders of granite are reduced to smaller, more manageable sizes to allow for easier transportation and further processing. The primary crusher is designed to handle the initial size reduction of large, hard rocks into more manageable sizes, typically ranging from 6 to 12 inches (150 mm to 300 mm) in diameter, depending on the machine and configuration.
Granite is a very hard material, often requiring heavy-duty equipment capable of handling extreme pressure and high impact. The primary crushing stage aims to reduce these large rocks to a size that can be processed by secondary crushers (like cone crushers or impact crushers) for finer reductions.
Types of Primary Crushing Equipment for Granite
Several types of crushers are used in the primary crushing of granite. The choice of equipment depends on factors such as the hardness of the rock, the desired output size, and the specific requirements of the quarry or processing plant. The most common types of primary crushers used for granite are:
1. Jaw Crushers
Jaw crushers are the most widely used primary crushers for granite. They are highly effective in reducing large granite blocks into smaller pieces, typically between 6 to 12 inches in size. The mechanism of jaw crushers involves a pair of jaws, one fixed and one movable, which crush the material by compressing it between the two surfaces.
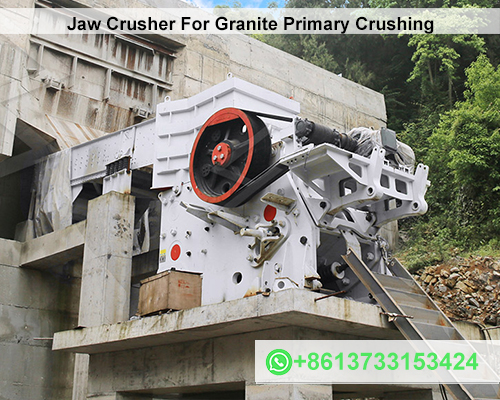
Advantages of Jaw Crushers for Granite:
- High Capacity: Jaw crushers are known for their ability to process large volumes of material in a short time.
- Versatility: They can handle a wide range of materials, including very hard stones like granite.
- Reliable Performance: Jaw crushers are durable and perform consistently under heavy-duty conditions, making them ideal for granite quarrying operations.
- Simple Operation: With minimal moving parts, jaw crushers are easy to operate and maintain, leading to lower operational costs.
Disadvantages of Jaw Crushers:
- Limited Particle Shape: While jaw crushers can reduce large pieces of granite into smaller sizes, they may not always produce uniform or cubical particles, which might be required for certain applications.
- High Wear and Tear: Jaw crushers can experience high wear and tear, especially when processing very hard materials like granite. This may require more frequent maintenance and part replacements.
2. Gyratory Crushers
Gyratory crushers are another type of primary crusher often used in large-scale granite processing plants. They operate on a similar principle to jaw crushers, but with a conical shape. The material is crushed between an eccentrically rotating spindle and a concave surface, which produces a similar reduction in size.
Advantages of Gyratory Crushers:
- Higher Capacity: Gyratory crushers can handle higher capacities than jaw crushers, making them ideal for large granite quarries.
- Better at Handling Larger Rocks: Gyratory crushers are well-suited for processing very large granite rocks, often exceeding the size limits of jaw crushers.
- Efficient Size Reduction: They typically provide a more consistent and uniform product size, making them suitable for secondary and tertiary crushing stages.
Disadvantages of Gyratory Crushers:
- Higher Cost: Gyratory crushers tend to have a higher initial cost and maintenance costs than jaw crushers.
- Complexity: Gyratory crushers have a more complex design and operation compared to jaw crushers, which can lead to more technical challenges in terms of installation and maintenance.
3. Impact Crushers
Impact crushers are often used as secondary crushers, but some can also be configured for primary crushing. These crushers use high-speed rotors to strike the granite, breaking it into smaller pieces. Although primarily used for softer rocks, impact crushers can be adapted to handle harder materials like granite by adjusting the rotor speed and other operational parameters.
Advantages of Impact Crushers for Granite:
- High Reduction Ratios: Impact crushers are capable of producing fine aggregates with high reduction ratios, making them useful for creating material with a smaller size.
- Good Particle Shape: Impact crushers are generally better at producing cubical or more uniformly shaped particles, which can be important in certain applications such as asphalt production.
- Less Maintenance: Compared to jaw and gyratory crushers, impact crushers can be less prone to wear and tear when processing granite.
Disadvantages of Impact Crushers:
- Less Suitable for Large Rocks: Impact crushers may not be the best option for the initial reduction of very large granite rocks, as they tend to be more effective at reducing smaller materials.
- Energy Consumption: Impact crushers typically require more energy to break down harder materials like granite compared to jaw or gyratory crushers.
4. Hammer Crushers
Hammer crushers, also known as hammer mills, are sometimes used in the primary crushing of granite, particularly in applications where a more compact, low-cost crushing system is needed. These crushers use rotating hammers mounted on a high-speed rotor to strike the material, breaking it into smaller pieces.
Advantages of Hammer Crushers:
- Cost-Effective: Hammer crushers are often less expensive than other types of primary crushers, making them a popular choice for smaller-scale operations.
- Simplicity: The simple design of hammer crushers makes them easy to operate and maintain.
- Effective for Softer Materials: While not the ideal choice for very hard granite, hammer crushers can handle softer variations of granite with lower abrasiveness.
Disadvantages of Hammer Crushers:
- Limited Capacity: Hammer crushers are generally not as efficient at handling large quantities of hard granite compared to jaw or gyratory crushers.
- Wear and Tear: The high-speed hammers can experience significant wear when processing very hard rocks, leading to increased maintenance and part replacements.
Conclusion
The primary crushing of granite is a crucial step in the overall granite processing workflow. The choice of equipment plays a significant role in determining the efficiency, output, and cost-effectiveness of the operation. Jaw crushers are the most widely used primary crushers for granite, offering a balance of reliability, capacity, and ease of maintenance. Gyratory crushers are better suited for large-scale operations requiring higher capacities, while impact crushers and hammer crushers provide options for secondary or specialized crushing needs.
Each type of primary crushing equipment has its own set of advantages and disadvantages, making it essential for granite processing plants to carefully consider their specific needs, including material characteristics, required output, and operational costs, when selecting the best equipment for their operations.