Granite Crushing and Screening Plant
Introduction to Granite Crushing and Screening Plants
Granite, a durable and versatile natural stone, is widely used in construction, road building, and infrastructure projects. To transform raw granite into usable aggregates, a granite crushing and screening plant plays a pivotal role. This guide explores the working principles, equipment, and advantages of these plants, ensuring you make informed decisions for your projects.
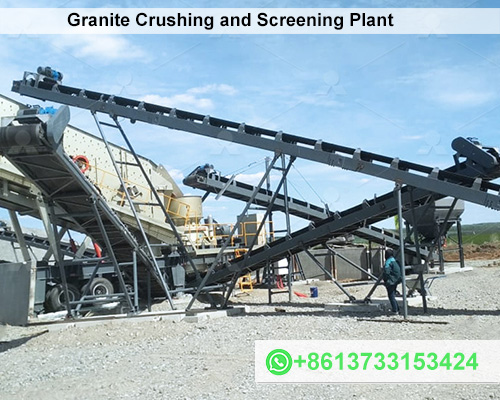
Key Components of a Granite Crushing and Screening Plant
- Primary Crushing Equipment
- Jaw Crusher:Ideal for breaking large granite blocks into manageable sizes (150–350 mm).
- Gyratory Crusher:Suited for high-capacity primary crushing in large-scale operations.
- Secondary and Tertiary Crushing
- Cone Crusher:Refine crushed granite into smaller, uniform particles (20–50 mm).
- Impact Crusher:Perfect for producing cubical-shaped aggregates for concrete and asphalt.
- Screening Machinery
- Vibrating Screens:Separate crushed granite into different sizes (e.g., 0–5 mm, 5–20 mm).
- Trommel Screens:Effective for washing and classifying aggregates in wet processing.
- Conveyors and Feeders
- Ensure seamless material transfer between crushing and screening stages.
Benefits of a Modern Granite Processing Plant
- High Efficiency:Automated systems reduce downtime and maximize output (up to 500–1,000 tons/hour).
- Cost Savings:Optimized energy consumption and minimal manual labor lower operational expenses.
- Eco-Friendly Design:Dust suppression systems and noise-reduction technologies meet environmental regulations.
- Versatility:Customizable configurations for producing aggregates, sand, or railway ballast.
Applications of Granite Aggregates
- Road Construction:Durable base layers and asphalt mixes.
- Concrete Production:High-strength aggregates for residential and commercial buildings.
- Landscaping:Decorative gravel and crushed stone for aesthetic projects.
- Railway Ballast:Stable foundation for rail tracks.
How to Choose the Right Granite Crushing Plant
- Assess Production Needs:Match plant capacity (TPH) to your project’s scale.
- Evaluate Site Conditions:Opt for mobile crusher for remote sites or fixed plants for long-term operations.
- Prioritize Quality Equipment:Brands like Sandvik, Metso, and Terex offer reliability and after-sales support.
- Focus on Sustainability:Look for energy-efficient motors and water recycling systems.
Conclusion
A well-designed granite crushing and screening plant is essential for producing high-quality aggregates efficiently. By integrating advanced technology and robust equipment, businesses can meet growing construction demands while adhering to environmental standards. For optimal results, partner with reputable suppliers who offer tailored solutions and maintenance services.