Iron Ore Crusher In Guinea
Guinea has abundant iron ore reserves, with an estimated total reserves of over 20 billion tons, accounting for about one-fifth of the world. Currently, the proven reserves are 6.5 billion tons, with an ore grade of up to 56-78%. Guinea’s iron ore mainly includes three types of ore: high-grade hematite, goethite hematite, and siliceous hematite.
Guinea’s iron ore is mainly distributed in the southern and central parts of the country, with the most concentrated area in the southeastern part of Guinea at the border with Liberia and C รด te d’Ivoire. The main mining areas include Ximangdu Iron Mine, Ningbashan Iron Mine, Zogota Mining Area, and Kalia Mining Area. Simandou is a world-class iron ore with reserves of approximately 1.8 billion tons and resources exceeding 4 billion tons, with an ore grade of over 65.5%. The ore deposit has an altitude of 1431-1658 meters and belongs to the Paleoproterozoic BIF type, with a length of approximately 110 kilometers.
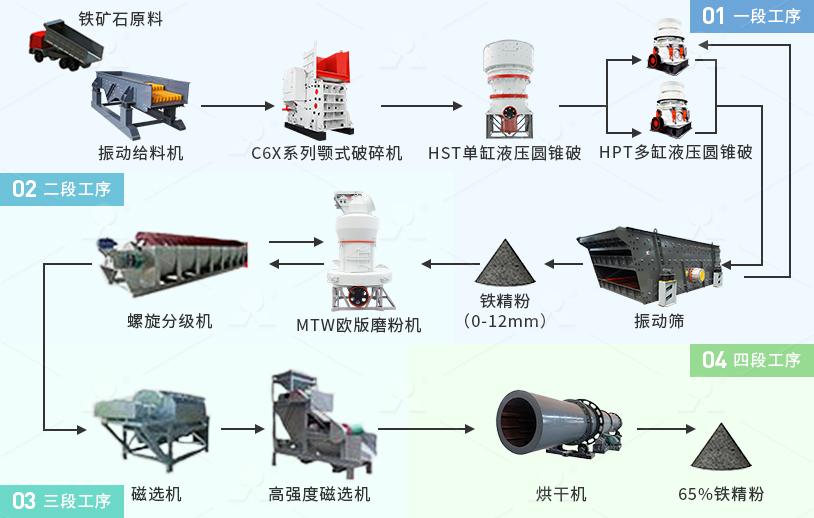
Liming Heavy Industry, a professional mining crushing solution provider, has been focusing on iron ore processing technology for 30 years, unveiling the mystery of the complete set of processing technology and solutions from iron ore to iron concentrate powder for you.
Iron ore process
Pure magnetite can be directly put into the furnace for ironmaking, but ultimately there is still a lot of accompanying ore. For some magnetite with high impurity content, simple crushing and screening, grinding and magnetic separation are required to produce concentrate. Therefore, the iron ore processing and production process mainly includes three processes: crushing, grinding, and beneficiation.
Phase 1: Crushing and screening – Three stage closed circuit crushing
Large blocks of iron ore are uniformly fed into the jaw crusher or coarse crushing mobile station by a vibrating feeder through the material bin for coarse crushing; After coarse crushing, the iron ore is sieved through a vibrating screen and then transported by a belt conveyor to a single cylinder hydraulic cone crusher for intermediate crushing; The iron ore material after intermediate crushing is sent to a multi cylinder hydraulic cone crusher for fine crushing;
Phase 2: Grinding powder
Uniformly feed the 0-12mm iron powder screened by the vibrating screen into the grinding machine for grinding, and screen it by the spiral classifier. If it does not meet the requirements, it will be sent to the grinding machine for further grinding;
Phase 3: Magnetic Separation
Send iron powder that meets the ore dressing requirements into a magnetic separator for strong magnetic separation and magnetic separation to remove impurities;
Stage 4: Drying
By feeding the obtained iron powder into a dryer for drying, iron concentrate powder can be obtained.