Iron Ore Crushing Mining Technology
Iron ore is an important raw material for steel production enterprises. Natural ore (iron ore) is gradually selected for iron through crushing, grinding, magnetic separation, flotation, and gravity separation. In theory, any ore containing iron elements or iron compounds can be called iron ore; however, in industry or commerce, iron ore is different from manganese ore. Iron ore not only needs to contain iron components, but also needs to have value for utilization. Iron exists in the form of compounds in nature, especially in the form of iron oxide, but with a lot of impurities. For example, hematite, magnetite, siderite, and limonite.
Iron ore processing production process
Iron ore is gradually extracted from iron ore through procedures such as crushing, grinding, magnetic separation, flotation, and gravity separation. Iron ore is a mineral aggregate containing iron element or iron compound that can be economically utilized.In the crushing and sorting of iron ore, the investment, consumables loss, and electricity consumption of crushing equipment and grinding equipment account for a large proportion. Therefore, the design of the ore beneficiation process must be efficient, concise, and economical. In the design of the crushing process, the principle of “more crushing and less grinding” is followed. The main process is multi-stage crushing with a jaw crusher, coarse cone crusher, fine cone crusher, and high-pressure roller mill. Auxiliary equipment such as magnetic separators, dryers, dust removal equipment, feeding systems, and dust collection devices can be added according to specific customer needs.
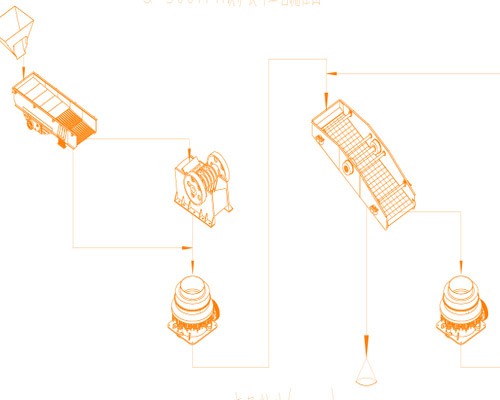
1: Crushing and screening
Large rocks or ores are uniformly and slowly fed into the jaw crusher (primary crushing) through a vibrating feeder from the storage bin. After coarse crushing, the rocks are screened by a vibrating screen and then sent to the cone crusher (secondary crushing) by a conveyor belt for further crushing. The materials crushed by the secondary crusher are screened by a vibrating screen to obtain finished products with a size of 0-10mm. Materials larger than 10mm are sent to the cone crusher (tertiary crushing) for fine crushing and then sent to the vibrating screen by a conveyor belt for screening, forming a cycle.
2: Grinding
The 0-12mm iron powder screened by the vibrating screen is evenly fed into the ball mill for grinding, and screened by the spiral classifier. The material that does not meet the requirements is sent back to the ball mill for further grinding.
The ball mill is a commonly used and efficient grinding equipment for grinding ores, such as iron ore, Iron ore, copper ore, lead-zinc ore, etc., in metal beneficiation, to grind the ore to below 0.075mm for subsequent beneficiation processes. According to the different discharge methods, it can be divided into grid type and overflow type. Its grinding methods can be divided into dry and wet grinding.
The spiral classifier, also known as the classifier, is one of the beneficiation equipment. The spiral classifier uses the principle that the solid particles have different specific gravity and therefore precipitate at different speeds in the liquid to perform mechanical classification. It can classify the powder from the mill according to the filtering, and then use the spiral blade to rotate into the mill feeding port for coarse material, and discharge the filtered fine material from the overflow pipe.
3: Flotation
The ground iron ore powder enters the magnetic separator for separation, and the separation section usually adopts a combination of strong magnetic separation and weak magnetic separation.
4: Drying
The iron powder after flotation is sent to the dryer. The drying process is mainly to remove the moisture of the selected iron powder in the beneficiation process to obtain high-quality iron powder.