Iron ore refinery processing plant in Malaysia
Iron ore is a rock and mineral that contains iron. It is one of the most important raw materials in the world, used to make steel. Steel is used in construction, transportation, and many other industries.
Malaysia is one of the world’s leading producers of iron ore. In 2020, the country produced 37.5 million tonnes of iron ore. The majority of iron ore in Malaysia is mined in the states of Pahang and Johor.
The iron ore processing plant in Malaysia is a large and complex facility. It uses a variety of processes to extract iron from the ore. The first step is to crush the ore into small pieces. The crushed ore is then ground into a fine powder. The powder is then mixed with water and chemicals to create a slurry. The slurry is pumped into a series of tanks, where it is subjected to a variety of processes to remove impurities. The final product is iron concentrate, which is a high-grade iron ore product.
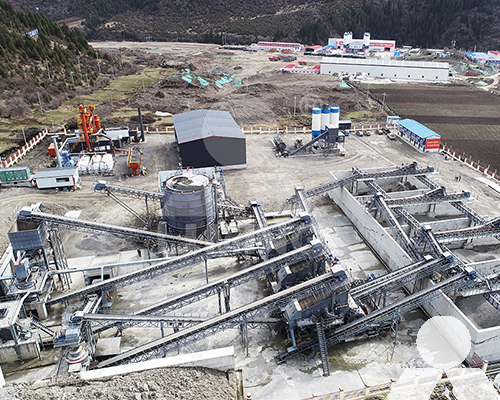
The iron concentrate is then shipped to steel mills around the world. The steel mills use the iron concentrate to make steel. Steel is a strong and versatile material that is used in a wide variety of applications.
The iron ore processing plant in Malaysia is a vital part of the global steel industry. It provides a high-quality iron ore product that is used to make steel around the world.
The iron ore processing plant in Malaysia
The iron ore processing plant in Malaysia is a large and complex facility that uses a variety of processes to extract iron from the ore. The plant is located in the state of Pahang, and it has a capacity of 3 million tonnes of iron ore per year.
The first step in the iron ore processing plant is to crush the ore into small pieces. The crushed ore is then ground into a fine powder. The powder is then mixed with water and chemicals to create a slurry. The slurry is pumped into a series of tanks, where it is subjected to a variety of processes to remove impurities.
The first process is called beneficiation. Beneficiation is a process that removes impurities from the iron ore. The most common beneficiation process is froth flotation. Froth flotation is a process that uses air bubbles to separate the iron ore from the impurities. The air bubbles attach to the iron ore particles, and they are then floated to the top of the tank. The impurities are left at the bottom of the tank.
The next process is called pelletizing. Pelletizing is a process that turns the iron ore powder into small balls. The balls are then fired in a kiln, which hardens them. The pelletized iron ore is then shipped to steel mills around the world.
The iron ore processing plant in Malaysia is a vital part of the global steel industry. It provides a high-quality iron ore product that is used to make steel around the world.
The future of the iron ore processing plant in Malaysia
The iron ore processing plant in Malaysia is facing a number of challenges. The most significant challenge is the declining global demand for steel. The global steel industry is in a state of decline, and this is having a negative impact on the demand for iron ore.
Another challenge facing the iron ore processing plant in Malaysia is the increasing competition from other countries. China is the world’s largest producer of iron ore, and it is increasing its production capacity. This is putting downward pressure on iron ore prices.
The iron ore processing plant in Malaysia is also facing environmental challenges. The plant produces a significant amount of waste, and this is having a negative impact on the environment.
The iron ore processing plant in Malaysia is facing a number of challenges, but it is also taking steps to address these challenges. The plant is investing in new technologies to improve its efficiency and reduce its environmental impact. The plant is also working to diversify its customer base.
The future of the iron ore processing plant in Malaysia is uncertain, but the plant is taking steps to ensure its long-term viability.