Hammer Crusher Design
Introduction
Hammer crusher is essential machines in various industries, particularly in mining, cement, and metallurgy. They are primarily used for crushing materials like coal, limestone, and gypsum into smaller pieces. This article explores the design aspects of hammer crusher, focusing on their structure, working principles, and factors influencing their performance.
Key Components of Hammer Crusher
1. Crusher Frame
The frame is the foundational structure of the hammer crusher. It must be robust enough to withstand the impact and vibration caused by the hammer’s movement. Generally made from high-strength steel, the frame should also provide adequate support for the rotor and other components.
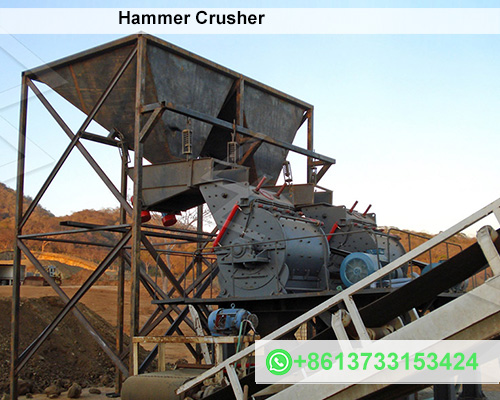
2. Rotor Assembly
The rotor is a critical component that houses the hammers. It rotates at high speed, imparting kinetic energy to the material being crushed. The design of the rotor should ensure balanced rotation, minimizing vibrations and enhancing efficiency. The choice of materials for the rotor is crucial; it often consists of high-alloy steel to withstand wear and tear.
3. Hammers
Hammers are the active elements of the crusher, responsible for the actual crushing action. They can be of various shapes and sizes, depending on the material to be processed. Common designs include:
- Fixed Hammers: These are stationary and provide a crushing surface against which the material impacts.
- Swinging Hammers: These rotate and strike the material, allowing for more effective crushing.
4. Screening Plate
The screening plate, located at the bottom of the crushing chamber, allows crushed material to exit the machine while retaining larger pieces. The design of this plate should facilitate efficient material flow and prevent clogging.
5. Drive Mechanism
The drive mechanism, often a motor coupled with gears or belts, provides the necessary power to the rotor. The design should ensure reliable operation with minimal maintenance, balancing speed and torque for optimal performance.
Working Principle
The hammer crusher operates on a simple principle: material is fed into the crushing chamber, where it is impacted by the rotating hammers. As the hammers strike the material, it is shattered into smaller pieces. The size of the final product can be controlled by adjusting the gap between the hammers and the screening plate.
Feed Process
- Material Feeding: Raw materials are fed into the crusher through a hopper.
- Crushing Action: The rotor spins, and the hammers collide with the material, causing it to break apart.
- Sizing and Discharge: Crushed material passes through the screening plate, while larger pieces are re-crushed until they reach the desired size.
Factors Influencing Hammer Crusher Design
1. Material Properties
The type of material being processed affects the design significantly. Harder materials may require more robust hammers and a stronger frame to withstand the impact.
2. Desired Output Size
The intended size of the crushed material determines the design of the screening plate and the spacing between the hammers and the plate.
3. Production Capacity
Designing a hammer crusher for a specific production capacity involves considering the rotor speed, hammer weight, and the size of the crushing chamber.
4. Energy Efficiency
Designing for energy efficiency can reduce operational costs. This involves optimizing the rotor design and ensuring the drive mechanism is efficient.
Conclusion
The design of a hammer crusher is crucial for its performance and longevity. By focusing on key components, understanding the working principle, and considering various influencing factors, engineers can create efficient and effective hammer crusher suited to specific industrial applications. As technology evolves, ongoing innovations in materials and design will continue to enhance the capabilities of these versatile machines.