Hammer Crusher in Mining
Mining is a complex industry that demands robust and efficient equipment to handle the extraction, processing, and transportation of valuable minerals. Among the machinery used in mining operations, the hammer crusher stands out as an essential tool for crushing rocks and minerals. Its simplicity, reliability, and versatility make it a popular choice across various mining sectors. This article delves into the role of the hammer crusher in mining, how it works, and its advantages and limitations.
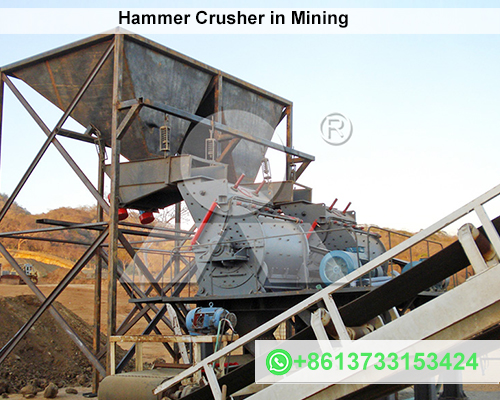
Overview of the Hammer Crusher
A hammer crusher is a machine designed to break down large rocks into smaller, more manageable sizes using high-speed rotary hammers. These crusher is typically employed for crushing medium to hard materials and can be used in various stages of mining operations, including the primary, secondary, and even tertiary crushing processes.
The hammer crusher’s basic design consists of:
- Rotary hammers attached to a rotating shaft or rotor.
- Impact plates or breaker plates that help break the material further as it is thrown against them by the hammers.
- A grate screen or grate bars located at the crusher’s base to allow the desired size of material to pass through.
Working Principle
The hammer crusher operates on the principle of impact. As the rotor spins at high speed, the hammers attached to it swing outward. When material is fed into the machine, it comes into contact with the rotating hammers and is broken by the impact force. The crushed material is then further impacted by the breaker plates and is forced through the grate bars, which control the size of the final product.
This method of crushing makes hammer crusher highly efficient for breaking down materials like limestone, coal, gypsum, shale, and other relatively soft materials. It is also ideal for creating uniform particles for further processing or direct use.
Types of Hammer Crusher
There are several types of hammer crusher used in mining, each suited to specific applications:
- Reversible Hammer Crusher: Capable of reversing the direction of rotor rotation, this crusher type can process materials with high moisture content without clogging.
- Non-Reversible Hammer Crusher: Often used for medium-hard materials, this crusher has a fixed direction of rotor rotation.
- Single-Stage Hammer Crusher: Commonly used for reducing large-sized materials in one step, eliminating the need for secondary crushing.
- Heavy Hammer Crusher: Known for its higher crushing ratio, this type is often employed in mining operations to crush hard rocks and ores.
Applications in Mining
Hammer crusher is primarily used in mining for the following tasks:
- Ore Reduction: Hammer crusher is employed to crush large ore blocks into smaller pieces for further processing, such as in ball mills or flotation cells.
- Breaking Down Overburden: Mining operations often require breaking down layers of soil, rock, and other overburden materials to reach valuable ore deposits. Hammer crusher is efficient for this task.
- Coal Processing: In coal mining, hammer crusher is widely used for crushing coal to the desired size before it is transported to the power plants or other processing facilities.
Advantages of Hammer Crusher
- Simple Structure: Hammer crusher have fewer mechanical components compared to other crusher, making them easier to maintain and repair.
- High Crushing Efficiency: Due to their impact-based operation, hammer crusher can process materials quickly and reduce them to a uniform size.
- Versatility: They can be used for both primary and secondary crushing stages, and for a wide range of materials.
- Low Investment Costs: Hammer crusher typically have lower capital costs than other types of crusher, such as cone crusher or jaw crusher.
- Adaptability to Moisture Content: Reversible hammer crusher, in particular, are designed to handle materials with higher moisture content without clogging.
Limitations of Hammer Crusher
Despite their numerous advantages, hammer crusher have certain limitations:
- Wear and Tear: Due to the impact nature of the crusher, the hammers and breaker plates experience high wear, leading to frequent replacements and increased maintenance costs.
- Limited to Medium-Hard Materials: Hammer crusher is not well-suited for crushing extremely hard materials, such as granite or basalt, which can cause excessive wear on the hammers.
- Size Control: The final particle size can be inconsistent if the screen grates wear unevenly or become clogged with material, leading to less precise output.
Maintenance Considerations
To ensure the longevity and optimal performance of a hammer crusher in mining applications, regular maintenance is crucial. Key maintenance tasks include:
- Checking and Replacing Worn Hammers: Due to the high-speed impact involved, hammers will wear out over time and must be inspected and replaced regularly.
- Monitoring Grate Bar Wear: The grate bars need to be maintained to ensure consistent output size and avoid clogging.
- Lubrication of Bearings and Rotating Parts: Proper lubrication reduces friction and wear on the moving components, extending the machine’s life.
Hammer crusher play an integral role in the mining industry by providing an efficient and cost-effective solution for breaking down medium to hard materials. Their simple structure, high crushing efficiency, and ability to handle various materials make them a popular choice for ore reduction and coal processing. While they do have some limitations, particularly concerning wear and tear, regular maintenance can help mitigate these issues. Overall, the hammer crusher is an essential tool that contributes to the efficiency and productivity of mining operations worldwide.