Granite sand manufacturing plant configuration
Setting up a granite sand manufacturing plant involves several key considerations, including the selection of location, equipment, and process flow. Here’s a suggested configuration for a granite sand manufacturing plant:
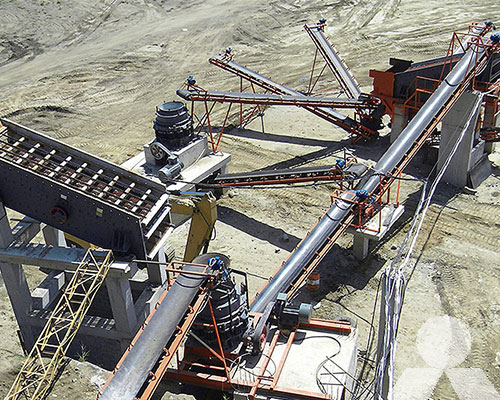
1.Location:
Choose a site with ample access to granite deposits, preferably close to the target market to minimize transportation costs.
Ensure availability of essential utilities like water and electricity.
2.Quarrying and Crushing:
Establish a granite quarry to extract raw granite blocks.
Use specialized machinery like diamond wire saws, excavators, and loaders for quarrying operations.
Crush the extracted granite blocks into smaller pieces using a primary crusher.
Use secondary and tertiary crushers to further reduce the size of the crushed granite.
3.Washing and Screening:
Install a granite washing system to remove impurities like clay, silt, and organic matter.
Set up a series of vibrating screens to classify the crushed granite into different sizes.
Use water to wash and separate the fine particles from the coarse aggregates.
Install a sand manufacturing unit to produce granite sand (also known as manufactured sand or M-sand).
Use a vertical shaft impact (VSI) crusher to shape and produce high-quality sand from the crushed granite.
Ensure that the VSI crusher is properly configured with the desired settings for gradation and particle shape.
5.Sand Washing and Dewatering:
Implement a sand washing and dewatering system to remove any remaining impurities and achieve the desired sand specifications.
Use a sand washer or hydrocyclone to clean the sand and separate fines.
Employ a dewatering screen or filter press to remove excess moisture from the washed sand.
6.Stockpiling and Storage:
Create designated stockpiles for different sizes of granite sand.
Implement a proper storage system to prevent contamination and maintain quality.
7.Quality Control:
Establish a laboratory to conduct regular quality control tests on the granite sand.
Monitor key parameters such as particle size distribution, silt content, moisture content, and chemical composition.
Implement quality assurance protocols to ensure compliance with relevant standards and customer requirements.
8.nvironmental Considerations:
Comply with environmental regulations and obtain necessary permits for the operation of the plant.
Implement dust control measures, such as dust suppression systems and enclosing conveyor transfer points.
Properly manage water usage, sedimentation ponds, and any potential runoff.
9.Maintenance and Safety:
Develop a maintenance plan for regular inspection and servicing of plant equipment.
Implement safety protocols to ensure the well-being of workers and prevent accidents.
10.Market and Logistics:
Conduct a market analysis to identify potential customers and demand for granite sand.
Establish a distribution network to supply the manufactured sand to construction sites, concrete plants, and other relevant customers.
Consider transportation logistics, including the availability of trucks or rail connections for product delivery.
Remember to consult with industry experts, engineers, and local authorities to ensure compliance with all regulations and to optimize your specific plant configuration.