Pebble
Last Updated :2023-07-14 Views:296
Choose jaw crusher or cone crusher in gravel work?
The choice between a jaw crusher and a cone crusher for gravel work depends on various factors such as the desired particle size, the feed size, the capacity requirements, and the abrasiveness of the material being crushed. Here are some considerations for each option:
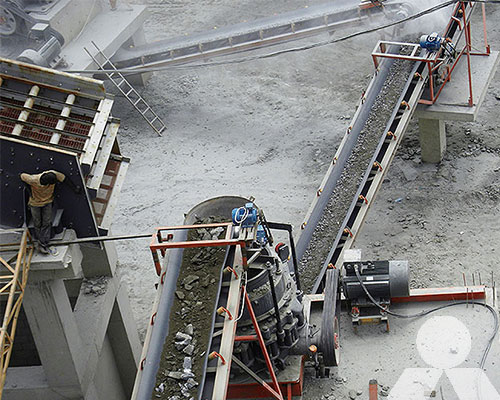
Jaw Crusher:
- Jaw crushers are commonly used in primary crushing stages and have a wider feeding opening compared to cone crushers.
- They are suitable for processing large-sized materials and can handle hard, abrasive materials effectively.
- Jaw crushers are generally more cost-effective than cone crushers in terms of initial purchase cost.
- They are ideal for achieving a cubic-shaped product with low fines content.
- However, jaw crushers have limitations in terms of the maximum feed size and the reduction ratio they can achieve.
Cone Crusher:
- Cone crushers are typically used in secondary and tertiary crushing stages.
- They have a conical-shaped crushing chamber that gradually narrows as it approaches the bottom.
- Cone crushers are suitable for processing smaller-sized materials and can produce finer product sizes compared to jaw crushers.
- They are often used for the production of high-quality aggregates.
- Cone crushers can handle a wide range of materials, including medium-hard to hard and abrasive ones.
- However, cone crushers are generally more expensive upfront and require regular maintenance.
In summary, if you need to process large-sized, hard, or abrasive materials, a jaw crusher might be the better choice. On the other hand, if you require finer product sizes or are working with smaller-sized materials, a cone crusher could be more suitable. It’s important to consider the specific requirements of your gravel work and consult with industry experts or equipment manufacturers to determine the best option for your needs.