Chromite ore beneficiation plant process flow
Chromite ore is a type of iron ore that contains significant amounts of chromium. It is a valuable mineral that is used in a variety of applications, including stainless steel production, refractory materials, and pigments.
Chromite ore beneficiation is the process of improving the grade and recovery of chromium from the ore. The goal of beneficiation is to produce a product that meets the specifications of the desired application.
There are a variety of beneficiation processes that can be used for chromite ore. The most common process is gravity separation, which uses the difference in density between chromium minerals and gangue minerals to separate the two. Gravity separation can be carried out using a variety of equipment, including shaking tables, jigs, and spirals.
Other beneficiation processes that can be used for chromite ore include magnetic separation, flotation, and chemical leaching. Magnetic separation uses the magnetic properties of chromium minerals to separate them from gangue minerals. Flotation uses the difference in surface wettability between chromium minerals and gangue minerals to separate the two. Chemical leaching uses chemical agents to dissolve chromium minerals from the ore.
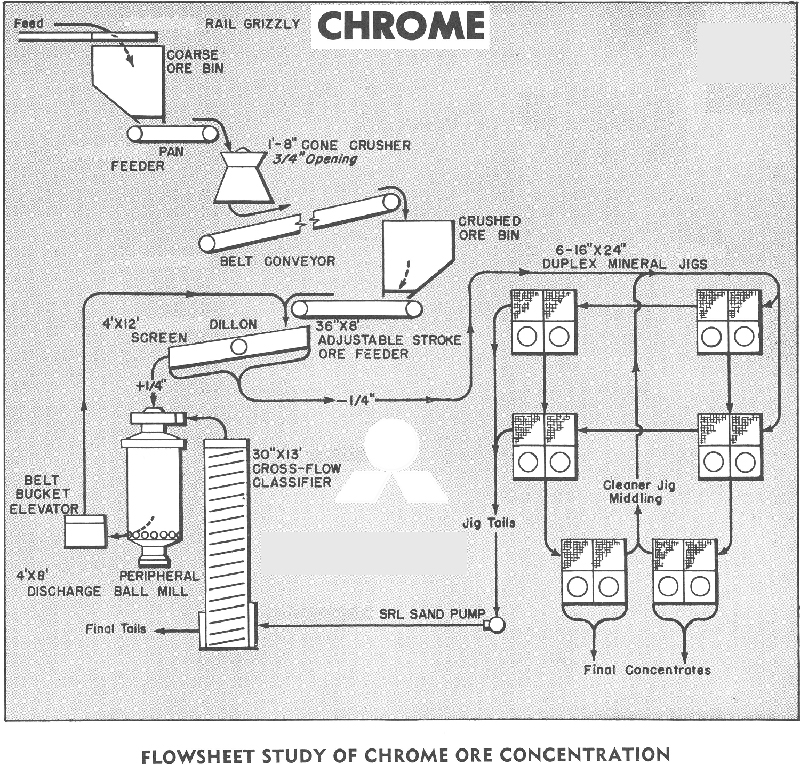
The specific beneficiation process that is used for a particular chromite ore deposit will depend on the characteristics of the ore. Factors that will be considered include the grade of the ore, the mineralogy of the ore, and the desired product specifications.
The following is a general flow diagram for a chromite ore beneficiation plant:
Raw ore * Crushing * Screening * Grinding * Gravity separation * Magnetic separation * Flotation * Chemical leaching * Product
Crushing and screening
The first step in chromite ore beneficiation is crushing and screening. The ore is crushed to a size of about 100 millimeters to facilitate subsequent processing. The crushed ore is then screened to remove oversized material.
Grinding
The crushed ore is then ground to a smaller size of about 100 micrometers. This is necessary to expose the chromium minerals and make them more amenable to beneficiation.
Gravity separation
Gravity separation is the most common beneficiation process for chromite ore. The ground ore is fed to a gravity separator, where it is subjected to a stream of water. The chromium minerals, which are denser than the gangue minerals, sink to the bottom of the separator. The gangue minerals float to the top and are removed.
Magnetic separation
Magnetic separation can be used to further improve the grade of the chromium concentrate produced by gravity separation. The chromium minerals in chromite ore are magnetic, so they can be separated from the gangue minerals using a magnetic separator.
Flotation
Flotation can be used to recover chromium from chromite ore that is too fine to be effectively processed by gravity separation. In flotation, the chromium minerals are coated with a surfactant that makes them hydrophobic. The hydrophobic chromium minerals are then floated to the surface of a flotation cell, where they are collected.
Chemical leaching
Chemical leaching can be used to recover chromium from chromite ore that is low in grade or that contains a high proportion of gangue minerals. In chemical leaching, the chromium minerals are dissolved from the ore using a chemical agent. The dissolved chromium can then be recovered by precipitation or other methods.
The final product of chromite ore beneficiation is a chromium concentrate that is typically 50% to 70% chromium. The chromium concentrate can then be further processed to produce high-purity chromium metal or other chromium-containing products.