Lead-zinc Ore Crushing Plant in Armenia
Armenia, known for its rich mineral resources, has historically been a significant producer of metals such as lead and zinc. A lead-zinc ore crushing plant is a facility designed to extract these valuable metals from the mined ore through a series of crushing, grinding, and concentration processes. While I can provide a general overview of such a plant, please note that the specific details and processes may vary depending on the technology and equipment used.
Ore Extraction: The lead-zinc ore is typically extracted from underground mines or open-pit mines. The extracted ore is transported to the crushing plant for further processing.
Primary Crushing: In the crushing plant, the ore is initially crushed into smaller pieces by a primary jaw crusher or gyratory crusher. This reduces the size of the ore to a manageable level and prepares it for further processing.
Secondary Crushing: The crushed ore from the primary crusher is then conveyed to a secondary cone crusher or impact crusher, where it is further reduced in size. This step ensures the ore is finely crushed to facilitate efficient grinding and subsequent mineral liberation.
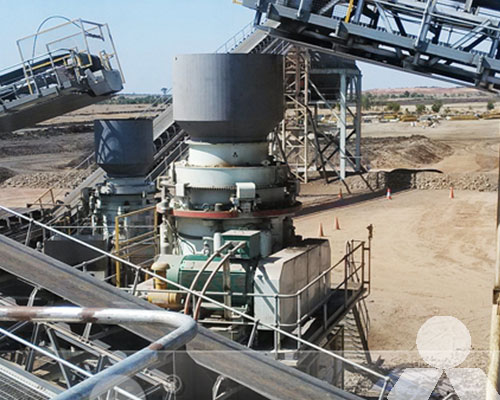
Grinding: The crushed ore is then transferred to a grinding mill, such as a ball mill or vertical roller mill, where it is mixed with water and grinding media. The grinding process reduces the ore particles to a fine size, allowing for the separation of valuable minerals from the gangue (unwanted materials).
Flotation: The ground ore, suspended in water, undergoes a flotation process. Chemical reagents are added to the mixture to selectively attach to the valuable minerals, such as lead and zinc sulfides. Air bubbles are introduced into the flotation cell, which carry the attached minerals to the surface, forming a froth layer.
Concentration: The froth containing the valuable minerals is skimmed off the top of the flotation cell, while the gangue sinks to the bottom. The collected froth is then further processed through a series of separation steps to obtain a concentrate rich in lead and zinc minerals.
Dewatering and Filtering: The concentrate is dewatered to reduce its moisture content, usually using thickeners and filters. This step prepares the concentrate for transportation and subsequent smelting or further refining processes.
Tailings Disposal: The remaining solid waste, known as tailings, is typically disposed of in tailings ponds or stored in designated areas. Various environmental measures are taken to ensure the safe and responsible management of tailings to minimize their impact on the surrounding ecosystem.
Smelting and Refining: The lead and zinc concentrates obtained from the crushing plant are further processed in smelters or refineries to produce pure metals. These processes involve high-temperature operations and the use of various chemical reactions to separate impurities and obtain marketable lead and zinc products.
It’s important to note that the above steps provide a general outline of a lead-zinc ore crushing plant. The actual plant design, equipment selection, and specific processes may vary depending on factors such as the characteristics of the ore, the desired end products, and the available technology and resources.